Chapter 9: Reservoirs, Strainers, Filters, and Accumulators
This page provides the chapter on hydraulic reservoirs, strainers, filters, and accumulators from the U.S. Navy's fluid power training course, NAVEDTRA 14105A, "Fluid Power," Naval Education and Training Professional Development and Technology Center, July 2015.
Other related chapters from the Navy's fluid power training course can be seen to the right.
Reservoirs, Strainers, Filters, and Accumulators
Fluid power systems must have a sufficient and continuous supply of uncontaminated fluid to operate efficiently. This chapter covers hydraulic reservoirs, various types of strainers and filters, and accumulators installed in fluid power systems.
Learning Objectives
When you have completed this chapter, you will be able to do the following:
- Recognize the functions and operating requirements of hydraulic reservoirs.
- Identify the types, characteristics, and construction features of hydraulic reservoirs.
- Identify the types, operating principles, and applications of accumulators.
- Recognize the types, functions, and construction features of filters and strainers.
- Recognize the operating characteristics of filters and strainers.
- Recognize the effects of foreign matter on filtration in a hydraulic power system.
- Recognize the functions and construction features of dehydrators.
- Recognize the operating characteristics of dehydrators.
Reservoirs
A hydraulic system must have a reserve of fluid in addition to that contained in the pumps, actuators, pipes, and other components of the system. This reserve fluid must be readily available to make up losses of fluid from the system, to make up for compression of the fluid under pressure, and to compensate for the loss of volume as the fluid cools. This extra fluid is contained in a tank usually called a reservoir. A reservoir may sometimes be referred to as a sump tank, a service tank, an operating tank, a supply tank, or a base tank.
In addition to providing storage for the reserve fluid needed for the system, the reservoir acts as a radiator for dissipating heat from the fluid and as a settling tank where heavy particles of contamination may settle out of the fluid and remain harmlessly on the bottom until removed by cleaning or flushing of the reservoir. Also, the reservoir allows entrained air to separate from the fluid.
Most reservoirs have a capped opening for filling, an air vent, an oil level indicator or dip stick, a return line connection, a pump inlet or suction line connection, a drain line connection, and a drain plug (Figure 9-1). The inside of the reservoir generally will have baffles to prevent excessive sloshing of the fluid and to put a partition between the fluid return line and the pump suction or inlet line. The partition forces the returning fluid to travel farther around the tank before being drawn back into the active system through the pump inlet line. This process aids in settling the contamination and separating the air from the fluid.
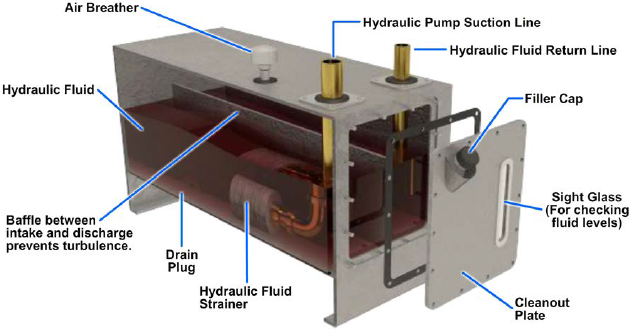
Large reservoirs are desirable for cooling. A large reservoir also reduces recirculation, which helps settle contamination and separate air. The ideal reservoir should be two to three times the pump output per minute. However, due to space limitations in mobile and aerospace systems, the benefits of a large reservoir may have to be sacrificed. But, they must be large enough to accommodate thermal expansion of the fluid and changes in fluid level due to system operation. Reservoirs are of two general types — nonpressurized and pressurized.
Nonpressurized Reservoirs
Nonpressurized reservoirs are used in several transport, patrol, and utility aircraft. These aircraft are not designed for violent maneuvers; in some cases, they do not fly at high altitudes. Those aircraft that incorporate nonpressurized reservoirs and fly at high altitudes have the reservoirs installed within a pressurized area. High altitude in this situation means an altitude where atmospheric pressure is inadequate to maintain sufficient flow of fluid to the hydraulic pumps. Most nonpressurized reservoirs are constructed in a cylindrical shape. The outer housing is manufactured from a strong corrosion-resistant metal.
Filter elements are normally installed internally within the reservoir to clean returning system hydraulic fluid. In some of the older aircraft, a filter bypass valve is incorporated to allow fluid to bypass the filter in the event the filter becomes clogged. Reservoirs serviced by pouring fluid directly into the reservoir have a filler strainer (finger strainer) assembly incorporated within the filler well to strain out impurities as the fluid enters the reservoir.
Generally, reservoirs described in the above paragraph use a visual gauge to indicate the fluid quantity. Gauges incorporated on or in the reservoir may be a glass tube, a direct reading gauge, or a float-type rod, which is visible through a transparent dome. In some cases, the fluid quantity may also be read in the cockpit through the use of quantity transmitters.
A typical nonpressurized reservoir is shown in Figure 9-2. This reservoir consists of a welded body and cover assembly clamped together. Gaskets are incorporated to seal against leakage between assemblies.
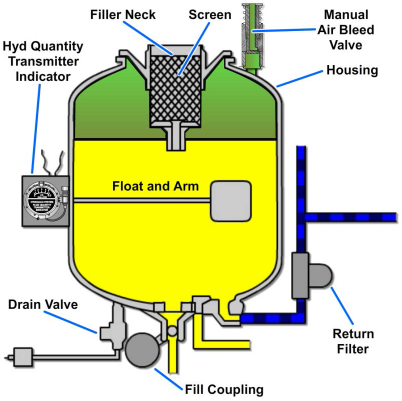
Pressurized Reservoirs
A pressurized reservoir is required in hydraulic systems where atmospheric pressure is insufficient to maintain a net positive suction head (NPSH) to the pump. There are two common types of pressurized reservoirs — fluid-pressurized and air-pressurized.
Fluid-Pressurized Reservoir
Some aircraft hydraulic systems use fluid pressure for pressurizing the reservoir. The reservoir shown in Figure 9-3 is of this type. This reservoir is divided into two chambers by a floating piston. The piston is forced downward in the reservoir by a compression spring within the pressurizing cylinder and by system pressure entering the pressurizing port of the cylinder.
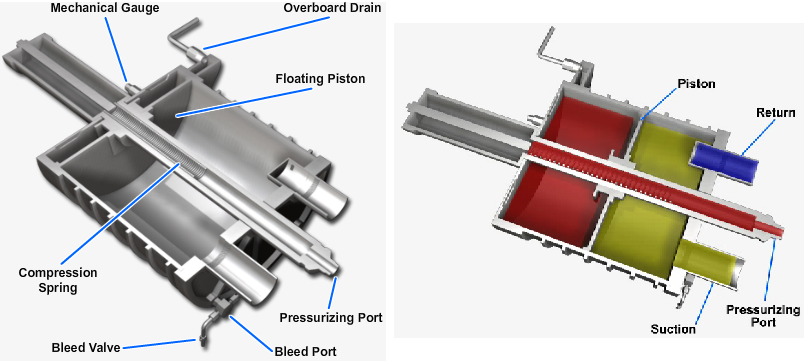
The pressurizing port is connected directly to the pressure line. When the system is pressurized, pressure enters the pressure port, thus pressurizing the reservoir. Pressure from the reservoir pressurizes the pump suction line and the reservoir return line to the same pressure.
The reservoir shown in Figure 9-3 has five ports — pump suction, return, pressurizing, overboard drain, and bleed. Fluid is supplied to the pump through the pump suction port. Fluid returns to the reservoir from the system through the return port. Pressure from the pump enters the pressurizing cylinder in the top of the reservoir through the pressurizing port. The overboard drain port is used to drain the reservoir during maintenance, and the bleed port is used as an aid when the reservoir is being serviced.
Air-Pressurized Reservoirs
Air-pressurized reservoirs are currently used in many high-performance naval aircraft. Figure 9-4 shows a hydraulic power system with an air-pressurized reservoir incorporated. This system is similar to the one found on many aircraft; however, for clarification in the discussion of the operation of the system, Figure 9-4 does not show all of the components between the reservoir and the pump.
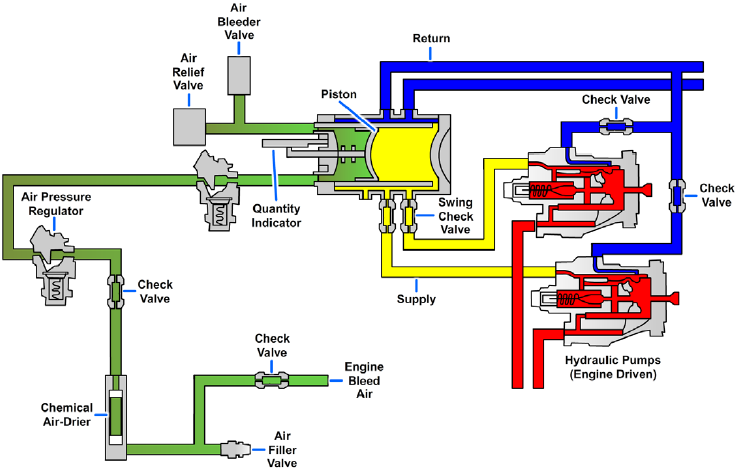
The reservoir is cylindrical in shape and has a piston installed internally to separate the air and fluid chambers. The piston rod end protrudes through the reservoir end cap and indicates the fluid quantity. The quantity indication may be seen by inspecting the distance the piston rod protrudes from the reservoir end cap. The reservoir has threaded openings for the connection of fittings and components. The schematic shown in Figure 9-4 shows several components installed in lines leading to and from the reservoir; however, this arrangement may not be the case in the actual installation. The air relief valve, bleeder valve, etc., may be installed directly on the reservoir. Because the reservoir is pressurized, it can normally be installed at any attitude and still maintain a positive flow of fluid to the pump.
Accumulators
An accumulator is a pressure storage reservoir in which hydraulic fluid is stored under pressure from an external source. The storage of fluid under pressure serves several purposes in hydraulic systems.
In some hydraulic systems it is necessary to maintain the system pressure within a specific pressure range for long periods of time. It is very difficult to maintain a closed system without some leakage, either external or internal. Even a small leak can cause a decrease in pressure. By using an accumulator, leakage can be compensated for and the system pressure can be maintained within an acceptable range for long periods of time. Accumulators also compensate for thermal expansion and contraction of the liquid due to variations in temperature.
A liquid, flowing at a high velocity in a pipe will create a backward surge when stopped suddenly by the closing of a valve. This sudden stoppage causes instantaneous pressures two to three times the operating pressure of the system. These pressures, or shocks, produce objectionable noise and vibrations, which can cause considerable damage to piping, fittings, and components. The incorporation of an accumulator enables such shocks and surges to be absorbed or cushioned by the entrapped gas, thereby reducing their effects. The accumulator also dampens pressure surges caused by pulsating delivery from the pump.
There are times when hydraulic systems require large volumes of liquid for short periods of time. This necessity is due to either the operation of large cylinders or the necessity of operating two or more circuits simultaneously. It is not economical to install a pump of such large capacity in the system for only intermittent usage, particularly if there is sufficient time during the working cycle for an accumulator to store up enough liquid to aid the pump during these peak demands.
The energy stored in accumulators may also be used to actuate hydraulically operated units if normal hydraulic system failure occurs. Four types of accumulators used in Navy hydraulic systems are as follows:
- Piston type.
- Bag or bladder type.
- Direct-contact gas-to-fluid.
- Diaphragm.
Piston-Type Accumulators
Piston-type accumulators consist of a cylindrical body called a barrel, closures on each end called heads, and an internal piston. The piston may be fitted with a tailrod, which extends through one end of the cylinder (Figure 9-5), or it may not have a tailrod at all (Figure 9-6). In the latter case, it is referred to as a floating piston. Hydraulic fluid is pumped into one end of the cylinder, and the piston is forced toward the opposite end of the cylinder against a captive charge of air or an inert gas, such as nitrogen. Sometimes the amount of air charge is limited to the volume within the accumulator; other installations may use separate air flasks, which are piped to the air side of the accumulator. Piston accumulators may be mounted in any position.
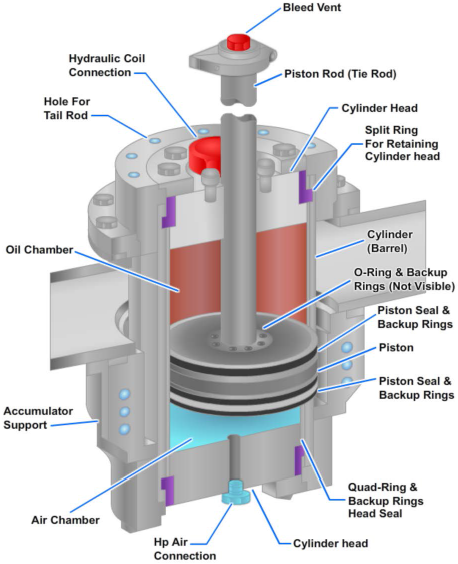
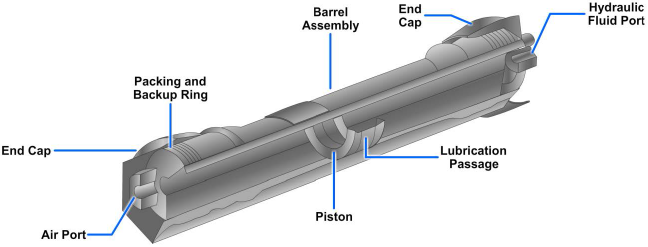
The gas portion of the accumulator may be located on either side of the piston. For example, in submarine hydraulic systems with tailrod pistons, the gas is usually on the bottom and the fluid on top; in surface ships with floating pistons, the gas is usually on the top. The orientation of the accumulator and the type of accumulator are based upon such criteria as available space, maintenance accessibility, size, need for external monitoring of the piston's location (tailrod indication), contamination tolerance, seal life, and safety. The purpose of the piston seals is to keep the fluid and the gas separate.
Usually, tailrod accumulators use two piston seals, one for the air side and one for the oil side, with the space between them vented to the atmosphere through a hole drilled the length of the tailrod. When the piston seals fail in this type of accumulator, air or oil leakage is apparent. However, seal failure in floating piston or nonvented tailrod accumulators will not be as obvious. Therefore, more frequent attention to venting or draining the air side is necessary. An indication of worn and leaking seals can be detected by the presence of significant amounts of oil in the air side.
Bladder-Type Accumulators
Bladder- or bag-type accumulators consist of a shell or case with a flexible bladder inside the shell (Figure 9-7). The bladder is larger in diameter at the top (near the air valve) and gradually tapers to a smaller diameter at the bottom. The synthetic rubber is thinner at the top of the bladder than at the bottom. The operation of the accumulator is based on Barlow's formula for hoop stress, which states: "The stress in a circle is directly proportional to its diameter and wall thickness." This means that for a certain thickness, a large-diameter circle will stretch faster than a small-diameter circle; or for a certain diameter, a thin wall hoop will stretch faster than a thick wall hoop. Thus, the bladder will stretch around the top at its largest diameter and thinnest wall thickness, and then will gradually stretch downward and push itself outward against the walls of the shell. As a result, the bladder is capable of squeezing out all the liquid from the accumulator. Consequently, the bladder accumulator has a very high volumetric efficiency. In other words, this type of accumulator is capable of supplying a large percentage of the stored fluid to do work.
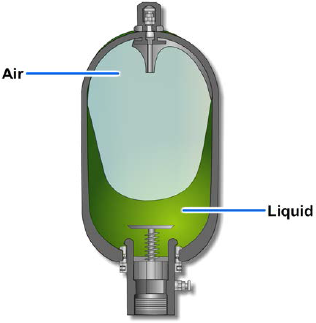
The bladder is precharged with air or inert gas to a specified pressure. Fluid is then forced into the area around the bladder, further compressing the gas in the bladder. This type of accumulator has the advantage that as long as the bladder is intact, there is no exposure of fluid to the gas charge and therefore less danger of an explosion.
Direct-Contact Gas-to-Fluid Accumulators
Direct-contact gas-to-fluid accumulators generally are used in very large installations where it would be very expensive to require a pistonor bladder-type accumulator. This type of accumulator consists of a fully enclosed cylinder, mounted in a vertical position, containing a liquid port on the bottom and a pneumatic charging port at the top (Figure 9-8). This type of accumulator is used in some airplane elevator hydraulic systems where several thousand gallons of fluid are needed to supplement the output of the hydraulic pumps for raising the elevator platform. The direct contact between the air or gas and the hydraulic fluid tends to entrain excessive amounts of gas in the fluid. For this reason, direct contact accumulators are generally not used for pressures over 1,200 per square inch (psi). The use of this type of accumulator with flammable fluid is dangerous because there is a possibility of explosion if any oxygen is present in the gas, and pressure surges generate excessive heat. For this reason, safety fluids are used in this type of installation.
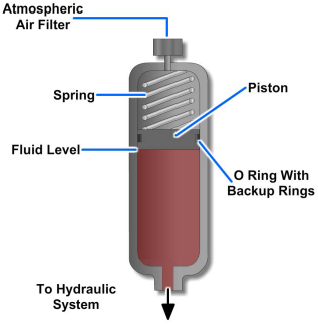
Diaphragm Accumulators
The diaphragm-type accumulator is constructed in two halves that are either screwed or bolted together. A synthetic rubber diaphragm is installed between both halves, making two chambers. Two threaded openings exist in the assembled component. The opening at the top, as shown in Figure 9-9, contains a screen disc that prevents the diaphragm from extruding through the threaded opening when system pressure is depleted, thus rupturing the diaphragm. On some designs the screen is replaced by a button-type protector fastened to the center of the diaphragm. An air valve for pressurizing the accumulator is located in the gas chamber end of the sphere, and the liquid port to the hydraulic system is located on the opposite end of the sphere. This accumulator operates in a manner similar to that of the bladder-type accumulator.
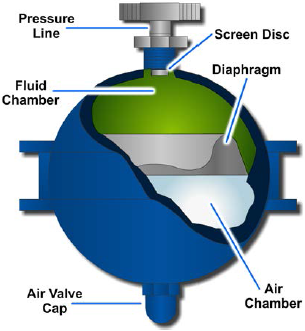
Filtration
You have learned that maintaining hydraulic fluids within allowable limits is crucial to the care and protection of hydraulic equipment. While every effort must be made to prevent contaminants from entering the system, contaminants that do find their way into the system must be removed. Filtration devices are installed at key points in fluid power systems to remove the contaminants that enter the system, along with those that are generated during normal operations.
Filtration devices for hydraulic systems differ somewhat from those of pneumatic systems. Therefore, they will be discussed separately. The filtering devices used in hydraulic systems are commonly referred to as strainers and filters. Because they share a common function, the terms strainer and filter are often used interchangeably. As a general rule, devices used to remove large particles of foreign matter from hydraulic fluids are referred to as strainers, while those used to remove the smallest particles are referred to as filters.
Strainers
Strainers are used primarily to catch only very large particles and will be found in applications where this type of protection is required. Most hydraulic systems have a strainer in the reservoir at the inlet to the suction line of the pump. A strainer is used in lieu of a filter to reduce its chance of being clogged and starving the pump. However, because this strainer is located in the reservoir, its maintenance is frequently neglected. When heavy dirt and sludge accumulate on the suction strainer, the pump soon begins to cavitate. Pump failure follows quickly.
Filters
The most common device installed in hydraulic systems to prevent foreign particles and contamination from remaining in the system is filters. They may be located in the reservoir, in the return line, in the pressure line, or in any other location in the system where the designer of the system decides they are needed to safeguard the system against impurities.
Filters are classified as full-flow and proportional or partial flow. In the full-flow type of filter, all the fluid that enters the unit passes through the filtering element, while in the proportional-flow type, only a portion of the fluid passes through the element.
Full-Flow Filter
The full-flow filter provides a positive filtering action; however, it offers resistance to flow, particularly when the element becomes dirty. Hydraulic fluid enters the filter through the inlet port in the body and flows around the filter element inside the filter bowl. Filtering takes place as the fluid passes through the filtering element and into the hollow core, leaving the dirt and impurities on the outside of the filter element. The filtered fluid then flows from the hollow core through the outlet port and into the system (Figure 9-10).
Some full-flow filters are equipped with a contamination indicator (Figure 9-11). These indicators, also known as differential pressure indicators, are available in three types — gauge indicators, mechanical pop-up indicators, and electrical with mechanical pop-up indicators. As contaminating particles collect on the filter element, the differential pressure across the element increases. In some installations using gauges as indicators, the differential pressure must be obtained by subtracting the readings of two gauges located somewhere along the filter inlet and outlet piping. For pop-up indicators, when the increase in pressure reaches a specific value, an indicator (usually in the filter head) pops out, signifying that the filter must be cleaned or replaced. To eliminate the possibility of false indications resulting from cold weather, a low-temperature lockout feature is installed in most pop-up types of contamination indicators. The pressure differential may be much higher with a cold fluid because of increased viscosity.
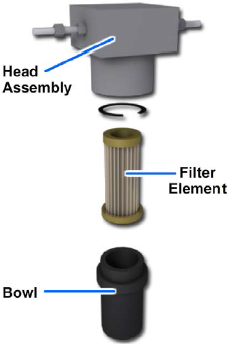
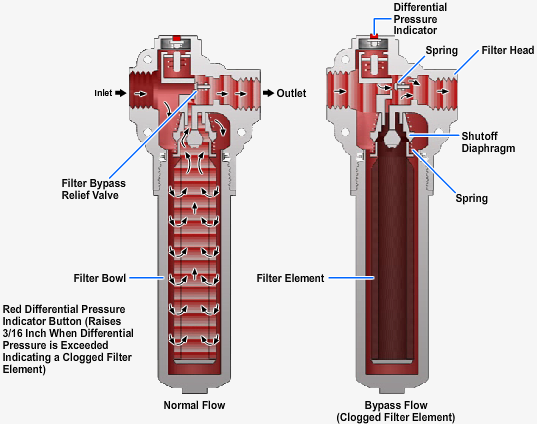
Filter elements used in filters that have a contamination indicator are not normally removed or replaced until the indicator is actuated. This procedure decreases the possibility of system contamination from outside sources due to unnecessary handling.
The use of the nonbypassing type of filter eliminates the possibility of contaminated fluid bypassing the filter element and contaminating the entire system. This type of filter will minimize the necessity for flushing the entire system and lessen the possibility of failure of pumps and other components in the system.
A bypass relief valve is installed in some filters. The bypass relief valve allows the fluid to bypass the filter element and pass directly through the outlet port in the event that the filter element becomes clogged. These filters may or may not be equipped with the contamination indicator. Figure 9-11 shows a full-flow bypass-type hydraulic filter with a contamination indicator.
A filter bypass indicator provides a positive indication, when activated, that fluid is bypassing the filter element by flowing through the bypass relief valve. This indicator should not be confused with the pop-up differential pressure indicator previously discussed, which simply monitors the pressure across the element. With the bypass indicator, a similar pop-up button is often used to signal that maintenance is needed. However, the bypass indicators further signal that, as a result of the high differential pressures across the element, an internal bypass relief valve has lifted and some of the fluid is bypassing the element.
Identification of the type of installed indicator can be obtained from filter manifold drawings or related equipment manuals. Both a fluid bypass indicator and a differential pressure indicator or gauge may be installed on the same filter assembly.
As with differential pressure indicators, bypass relief indicators can be activated by pressure surges. On some relief indicators, the pop-up button, or whatever signal device is used, will return to a normal position when the surge passes and pressure is reduced. Other relief indicators may continue to indicate a bypass condition until they are manually reset. Before taking corrective action based on indicator readings, verify the bypass condition at normal operating temperature and flow conditions by attempting to reset the indicator.
Proportional-Flow Filter
This type of filter operates on the venturi principle. As the fluid passes through the venturi throat, a drop in pressure is created at the narrowest point (Figure 9-12). A portion of the fluid flowing toward and away from the throat of the venturi flows through the passages into the body of the filter. A fluid passage connects the hollow core of the filter with the throat of the venturi. Thus, the low-pressure area at the throat of the venturi causes the fluid under pressure in the body of the filter to flow through the filter element, through the hollow core, into the low-pressure area, and then return to the system. Although only a portion of the fluid is filtered during each cycle, constant recirculation through the system will eventually cause all the fluid to pass through the filter element.
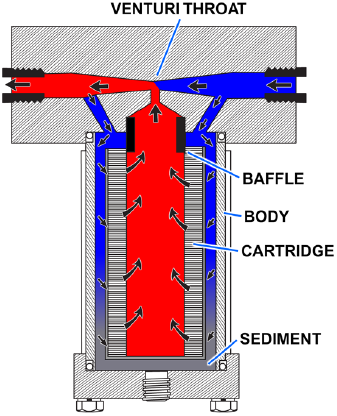
Filter Rating
Filters have three ratings — absolute, mean, and nominal. The absolute filtration rating is the diameter in microns of the largest spherical particle that will pass through the filter under a certain test condition. This rating is an indication of the largest opening in the filter element. The mean filtration rating is the measurement of the average size of the openings in the filter element. The nominal filtration rating is usually interpreted to mean the size of the smallest particles, of which 90 percent will be trapped in the filter at each pass through the filter.
Filter Elements
Filter elements generally may be divided into two classes — surface and depth. Surface filters are made of closely woven fabric or treated paper with a uniform pore size. Fluid flows through the pores of the filter material, and contaminants are stopped on the filter's surface. This type of element is designed to prevent the passage of a high percentage of solids of a specific size. Depth filters, on the other hand, are composed of layers of fabric or fibers that provide many tortuous paths for the fluid to flow through. The pores or passages must be larger than the rated size of the filter if particles are to be retained in the depth of the media rather than on the surface. Consequently, there is a statistical probability that a rather large particle may pass through a depth-type filter.
Filter elements may be of the 5-micron, woven mesh, micronic, porous metal, or magnetic type. The micronic and 5-micron elements have noncleanable filter media and are disposed of when they are removed. Porous metal, woven mesh, and magnetic filter elements are usually designed to be cleaned and reused.
5-Micron Noncleanable Filter Elements
The most common 5-micron filter medium is composed of organic and inorganic fibers integrally bonded by epoxy resin and faced with a metallic mesh upstream and downstream for protection and added mechanical strength. Filters of this type are not to be cleaned under any circumstances and will be marked Disposable or Noncleanable.
Another 5-micron filter medium uses layers of very fine stainless-steel fibers drawn into a random but controlled matrix. Filter elements of this material may be either cleanable or noncleanable, depending upon their construction.
Woven Wire-Mesh Filter Elements
Filters of this type are made of stainless steel and are generally rated as 15 or 25 microns (absolute). Figure 9-13 shows a magnified cross section of a woven wire-mesh filter element. This type of filter is reusable.
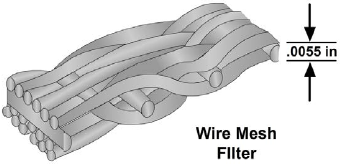
Micronic Hydraulic Filter Element
The term micronic is derived from the word micron. It could be used to describe any filter element; however, through usage, this term has become associated with a specific filter with a filtering element made of a specially treated cellulose paper (Figure 9-14). The filter shown in Figure 9-10 is a typical micronic hydraulic filter. The micronic filter element is designed to remove 99 percent of all particles 10 to 20 microns in diameter or larger. The replaceable element is made of specially treated convolutions (wrinkles) to increase its dirt-holding capacity. The element is noncleanable and should be replaced with a new filter element during maintenance inspections.
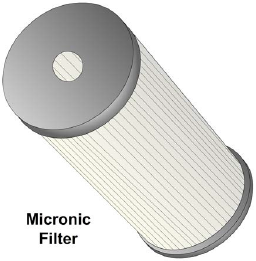
Magnetic Filters
Some hydraulic systems have magnetic filters installed at strategic points. Filters of this type are designed primarily to trap any ferrous particles that may be in the system.
Pneumatic Gases
Clean, dry gas is required for the efficient operation of pneumatic systems. Due to the normal conditions of the atmosphere, free air seldom satisfies these requirements adequately. The atmosphere contains both dust and impurities in various amounts and a substantial amount of moisture in vapor form.
Solids, such as, dust, rust, or pipe scale in pneumatic systems may lead to excessive wear and failure of components and in some cases, may prevent the pneumatic devices from operating. Moisture is also very harmful to the system. It washes lubrication from moving parts, thereby aiding corrosion and causing excessive wear of components. Moisture will also settle in low spots in the system and freeze during cold weather, causing a stoppage of the system or ruptured lines.
An ideal filter would remove all dirt and moisture from a pneumatic system without causing a pressure drop in the process. Obviously, such a condition can only be approached; it cannot be attained.
Removal of Solids
The removal of solids from the gas of pneumatic systems is generally done by screening (filtering), centrifugal force, or a combination of the two. In some cases, the removal of moisture is done in conjunction with the removal of solids.
Some types of air filters are similar in design and operation to the hydraulic filters discussed earlier. Some materials used in the construction of elements for air filters are woven screen wire, steel wool, fiberglass, and felt fabrics. Elements made of these materials are often used in the unit that filters the air as it enters the compressor.
Porous metal and ceramic elements are commonly used in filters that are installed in the compressed air supply lines. These filters also use a controlled air path to provide some filtration. Internal design causes the air to flow in a circular path within the bowl (Figure 9-15). Heavy particles and water droplets are thrown out of the airstream and drop to the bottom of the bowl. The air then flows through the filter element, which filters out most of the smaller particles. This type of filter is designed with a drain valve at the bottom of the bowl.
An air filter that uses moving mechanical devices as an element is illustrated in Figure 9-16. As compressed air passes through the filter, the force revolves a number of multiblade rotors at high speed. Moisture and dirt are caught on the blades of the rotors. The whirling blades hurl the impurities by centrifugal force to the outer rims of the rotors and to the inner walls of the filter housing. Here, contaminating matter is out of the airstream and falls to the bottom of the bowl, where it must be drained at periodic intervals.
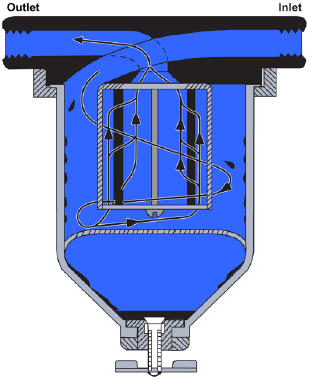
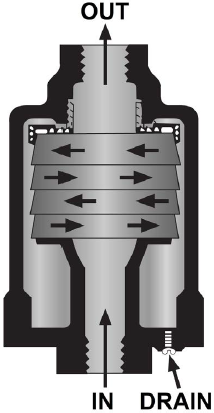
Removal of Moisture
The removal of moisture from compressed air is important for a compressed air system. If air at atmospheric pressure, even at a very low relative humidity, is compressed to 3,000 or 4,500 pounds psi, it becomes saturated with water vapor. Some moisture is removed by the intercoolers and aftercoolers. Also, air flasks, receivers, and banks are provided with low point drains to allow periodic draining of any collected moisture. However, many uses of air require air with an even smaller moisture content than can be obtained through these methods. Moisture in air lines can create problems that are potentially hazardous, such as the freezing of valves and controls. Freezing can occur, for example, if air at an extremely high pressure is throttled to a very low pressure at a high flow rate. The venturi effect of the throttled air produces very low temperatures, which will cause any moisture in the air to freeze into ice. Ice makes the valve (especially an automatic valve) either very difficult or impossible to operate. Also, droplets of water can cause serious water hammer in an air system that has high pressure and a high flow rate, and can cause corrosion, rust, and dilution of lubricants within the system. For these reasons, air driers (dehydrator, air purifier, and desiccator are all terms used by different manufacturers to identify these components) are used to dry the compressed air. Some water removal devices are similar in design and operation to the filters, shown in Figures 9-16 and 9-17. Two basic types of air dehydrators are the refrigerated and the desiccant types.
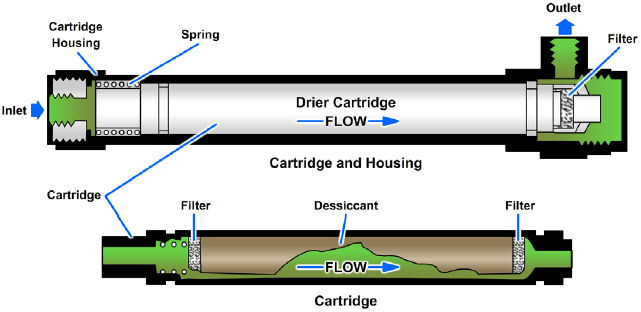
Refrigerated-Type Dehydrators
In refrigerated-type dehydrators, compressed air is passed over a set of refrigerated cooling coils. Oil and moisture vapors condense from the air and can be collected and removed via a low point drain.
Desiccant-Type Dehydrators
A desiccant is a chemical substance with a high capacity to absorb water or moisture. It also has the capacity to give off that moisture so that the desiccant can be reused.
Some compressed air system dehydrators use a pair of desiccant towers (flasks full of desiccant). One is kept in service dehydrating the compressed air, while the other one is being reactivated. A desiccant tower is normally reactivated by passing dry, heated air through it in the direction opposite the normal dehydration airflow.
Chemical Air Drier
Chemical air driers are installed in air systems to absorb moisture that may collect from air entering the system. The main parts of the air drier, shown in Figure 9-17, are the housing, the desiccant cartridge, the filter (porous bronze), and the spring. To ensure proper filtering, the air must pass through the air drier in the proper direction. The correct direction of flow is indicated by an arrow and the word flow printed on the side of the cartridge.
PDH Classroom offers a continuing education course based on this reservoirs, strainers, filters, and accumulators reference page. This course can be used to fulfill PDH credit requirements for maintaining your PE license.
Now that you've read this reference page, earn credit for it!