Head Loss
This page provides the chapter on head loss from the "DOE Fundamentals Handbook: Thermodynamics, Heat Transfer, and Fluid Flow," DOE-HDBK-1012/3-92, U.S. Department of Energy, June 1992.
Other related chapters from the "DOE Fundamentals Handbook: Thermodynamics, Heat Transfer, and Fluid Flow" can be seen to the right.
Head Loss
The head loss that occurs in pipes is dependent on the flow velocity, pipe length and diameter, and a friction factor based on the roughness of the pipe and the Reynolds number of the flow. The head loss that occurs in the components of a flow path can be correlated to a piping length that would cause an equivalent head loss.
Head Loss
Head loss is a measure of the reduction in the total head (sum of elevation head, velocity head and pressure head) of the fluid as it moves through a fluid system. Head loss is unavoidable in real fluids. It is present because of: the friction between the fluid and the walls of the pipe; the friction between adjacent fluid particles as they move relative to one another; and the turbulence caused whenever the flow is redirected or affected in any way by such components as piping entrances and exits, pumps, valves, flow reducers, and fittings.
Frictional loss is that part of the total head loss that occurs as the fluid flows through straight pipes. The head loss for fluid flow is directly proportional to the length of pipe, the square of the fluid velocity, and a term accounting for fluid friction called the friction factor. The head loss is inversely proportional to the diameter of the pipe.
$$ \text{Head Loss} \propto f ~{L ~v^2 \over D} $$Friction Factor
The friction factor has been determined to depend on the Reynolds number for the flow and the degree of roughness of the pipe's inner surface.
The quantity used to measure the roughness of the pipe is called the relative roughness, which equals the average height of surface irregularities (ε) divided by the pipe diameter (D).
$$ \text{Relative Roughness} = {\varepsilon \over D} $$The value of the friction factor is usually obtained from the Moody Chart, an example of which is shown below. The Moody Chart can be used to determine the friction factor based on the Reynolds number and the relative roughness.
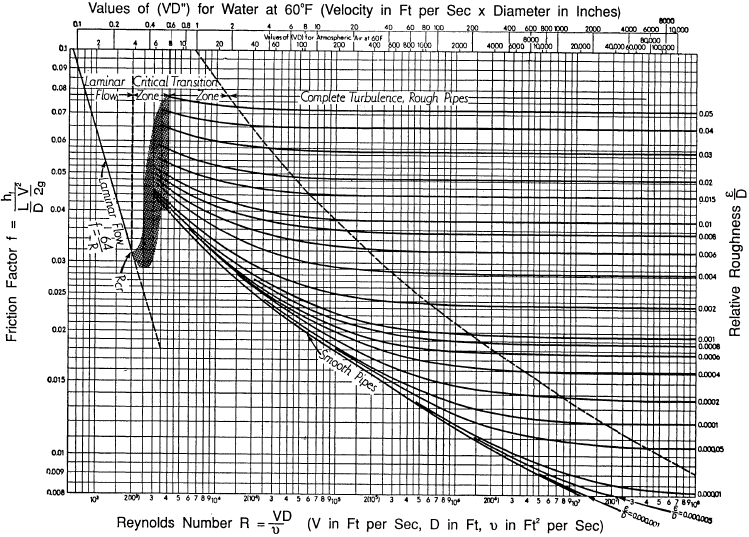
Example:
Determine the friction factor (f) for fluid flow in a pipe that has a Reynolds number of 40,000 and a relative roughness of 0.01.
Solution:
Using the Moody Chart, a Reynolds number of 40,000 intersects the curve corresponding to a relative roughness of 0.01 at a friction factor of 0.04.
PDH Classroom offers a continuing education course based on this head loss reference page. This course can be used to fulfill PDH credit requirements for maintaining your PE license.
Now that you've read this reference page, earn credit for it!
Darcy's Equation
The frictional head loss can be calculated using a mathematical relationship that is known as Darcy's equation for head loss. The equation takes two distinct forms. The first form of Darcy's equation determines the losses in the system associated with the length of the pipe.
where:
f | = | friction factor (unitless) |
L | = | length of pipe (ft) |
D | = | diameter of pipe (ft) |
v | = | fluid velocity (ft/sec) |
g | = | gravitational acceleration (ft/sec2) |
Example: Darcy's Head Loss Equation
A pipe 100 feet long and 20 inches in diameter contains water at 200°F flowing at a mass flow rate of 700 lbm/sec. The water has a density of 60 lbm/ft3 and a viscosity of 1.978×10-7 lbf-sec/ft2. The relative roughness of the pipe is 0.00008. Calculate the head loss for the pipe.
Solution:
The sequence of steps necessary to solve this problem is first to determine the flow velocity. Second, using the flow velocity and the fluid properties given, calculate the Reynolds number. Third, determine the friction factor from the Reynolds number and the relative roughness. Finally, use Darcy's equation to determine the head loss.
Use the Moody Chart for a Reynolds number of 8.4×107 and a relative roughness of 0.00008.
f = 0.012
$$ \begin{eqnarray} H_f &=& f ~{L \over D} ~{v^2 \over 2 ~g} \nonumber \\ &=& (0.012) ~{ 100 ~\text{ft} \over 20 ~\text{in} \left({1 ~\text{ft} \over 12 ~\text{in}}\right) } \cdot { \left(5.35 ~{\text{ft} \over \text{sec}}\right)^2 \over 2 \left(32.17 ~{\text{ft} \over \text{sec}^2}\right) } \nonumber \\ H_f &=& 0.32 ~\text{ft} \end{eqnarray} $$Minor Losses
The losses that occur in pipelines due to bends, elbows, joints, valves, etc. are sometimes called minor losses. This is a misnomer because in many cases these losses are more important than the losses due to pipe friction, considered in the preceding section. For all minor losses in turbulent flow, the head loss varies as the square of the velocity. Thus a convenient method of expressing the minor losses in flow is by means of a loss coefficient (k). Values of the loss coefficient (k) for typical situations and fittings is found in standard handbooks. The form of Darcy's equation used to calculate minor losses of individual fluid system components is expressed by Equation 3-15.
Equivalent Piping Length
Minor losses may be expressed in terms of the equivalent length (Leq) of pipe that would have the same head loss for the same discharge flow rate. This relationship can be found by setting the two forms of Darcy's equation equal to each other.
$$ f ~{L \over D} ~{v^2 \over 2 ~g} = k ~{v^2 \over 2 g} $$This yields two relationships that are useful.
Typical values of Leq/D for common piping system components are listed in Table 1. The equivalent length of piping that will cause the same head loss as a particular component can be determined by multiplying the value of Leq/D for that component by the diameter of the pipe. The higher the value of Leq/D, the longer the equivalent length of pipe.
Item | Leq/D |
---|---|
Globe Valve | |
Conventional | 400 |
Y-Pattern | 160 |
Gate Valve | |
Fully Open | 10 |
75% Open | 35 |
50% Open | 150 |
25% Open | 900 |
Standard Tee | |
Flow through Run | 10 |
Flow through Branch | 60 |
90° Standard Elbow | 30 |
45° Standard Elbow | 16 |
Return Bend | 50 |
Example:
A fully-open gate valve is in a pipe with a diameter of 10 inches. What equivalent length of pipe would cause the same head loss as the gate valve?
Solution:
From Table 1, we find that the value of Leq/D for a fully-open gate valve is 10.
Leq = (Leq/D) D
= 10 (10 inches)
= 100 inches
By adding the equivalent lengths of all components to the actual length of pipe in a system we can obtain the Leq value for the entire piping system.
PDH Classroom offers a continuing education course based on this head loss reference page. This course can be used to fulfill PDH credit requirements for maintaining your PE license.
Now that you've read this reference page, earn credit for it!