Boiling Heat Transfer
This page provides the chapter on boiling heat transfer from the "DOE Fundamentals Handbook: Thermodynamics, Heat Transfer, and Fluid Flow," DOE-HDBK-1012/2-92, U.S. Department of Energy, June 1992.
Other related chapters from the "DOE Fundamentals Handbook: Thermodynamics, Heat Transfer, and Fluid Flow" can be seen to the right.
Boiling Heat Transfer
The formation of steam bubbles along a heat transfer surface has a significant effect on the overall heat transfer rate.
Boiling
In a nuclear facility, convective heat transfer is used to remove heat from a heat transfer surface. The liquid used for cooling is usually in a compressed state, (that is, a subcooled fluid) at pressures higher than the normal saturation pressure for the given temperature. Under certain conditions, some type of boiling (usually nucleate boiling) can take place. It is advisable, therefore, to study the process of boiling as it applies to the nuclear field when discussing convection heat transfer.
More than one type of boiling can take place within a nuclear facility, especially if there is a rapid loss of coolant pressure. A discussion of the boiling processes, specifically local and bulk boiling, will help the student understand these processes and provide a clearer picture of why bulk boiling (specifically film boiling) is to be avoided in nuclear facility operations.
Nucleate Boiling
The most common type of local boiling encountered in nuclear facilities is nucleate boiling. In nucleate boiling, steam bubbles form at the heat transfer surface and then break away and are carried into the main stream of the fluid. Such movement enhances heat transfer because the heat generated at the surface is carried directly into the fluid stream. Once in the main fluid stream, the bubbles collapse because the bulk temperature of the fluid is not as high as the heat transfer surface temperature where the bubbles were created. This heat transfer process is sometimes desirable because the energy created at the heat transfer surface is quickly and efficiently "carried" away.
Bulk Boiling
As system temperature increases or system pressure drops, the bulk fluid can reach saturation conditions. At this point, the bubbles entering the coolant channel will not collapse. The bubbles will tend to join together and form bigger steam bubbles. This phenomenon is referred to as bulk boiling. Bulk boiling can provide adequate heat transfer provided that the steam bubbles are carried away from the heat transfer surface and the surface is continually wetted with liquid water. When this cannot occur film boiling results.
Film Boiling
When the pressure of a system drops or the flow decreases, the bubbles cannot escape as quickly from the heat transfer surface. Likewise, if the temperature of the heat transfer surface is increased, more bubbles are created. As the temperature continues to increase, more bubbles are formed than can be efficiently carried away. The bubbles grow and group together, covering small areas of the heat transfer surface with a film of steam. This is known as partial film boiling. Since steam has a lower convective heat transfer coefficient than water, the steam patches on the heat transfer surface act to insulate the surface making heat transfer more difficult. As the area of the heat transfer surface covered with steam increases, the temperature of the surface increases dramatically, while the heat flux from the surface decreases. This unstable situation continues until the affected surface is covered by a stable blanket of steam, preventing contact between the heat transfer surface and the liquid in the center of the flow channel. The condition after the stable steam blanket has formed is referred to as film boiling.
The process of going from nucleate boiling to film boiling is graphically represented in Figure 13. The figure illustrates the effect of boiling on the relationship between the heat flux and the temperature difference between the heat transfer surface and the fluid passing it.
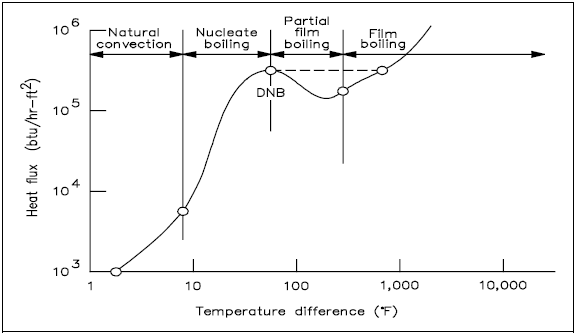
Four regions are represented in Figure 13. The first and second regions show that as heat flux increases, the temperature difference (surface to fluid) does not change very much. Better heat transfer occurs during nucleate boiling than during natural convection. As the heat flux increases, the bubbles become numerous enough that partial film boiling (part of the surface being blanketed with bubbles) occurs. This region is characterized by an increase in temperature difference and a decrease in heat flux. The increase in temperature difference thus causes total film boiling, in which steam completely blankets the heat transfer surface.
Departure from Nucleate Boiling and Critical Heat Flux
In practice, if the heat flux is increased, the transition from nucleate boiling to film boiling occurs suddenly, and the temperature difference increases rapidly, as shown by the dashed line in the figure. The point of transition from nucleate boiling to film boiling is called the point of departure from nucleate boiling, commonly written as DNB. The heat flux associated with DNB is commonly called the critical heat flux (CHF). In many applications, CHF is an important parameter.
For example, in a reactor, if the critical heat flux is exceeded and DNB occurs at any location in the core, the temperature difference required to transfer the heat being produced from the surface of the fuel rod to the reactor coolant increases greatly. If, as could be the case, the temperature increase causes the fuel rod to exceed its design limits, a failure will occur.
The amount of heat transfer by convection can only be determined after the local heat transfer coefficient is determined. Such determination must be based on available experimental data. After experimental data has been correlated by dimensional analysis, it is a general practice to write an equation for the curve that has been drawn through the data and to compare experimental results with those obtained by analytical means. In the application of any empirical equation for forced convection to practical problems, it is important for the student to bear in mind that the predicted values of heat transfer coefficient are not exact. The values of heat transfer coefficients used by students may differ considerably from one student to another, depending on what source "book" the student has used to obtain the information. In turbulent and laminar flow, the accuracy of a heat transfer coefficient predicted from any available equation or graph may be no better than 30%.