Chapter 3: Hydraulic Fluids
This page provides the chapter on hydraulic fluids from the U.S. Navy's fluid power training course, NAVEDTRA 14105A, "Fluid Power," Naval Education and Training Professional Development and Technology Center, July 2015.
Other related chapters from the Navy's fluid power training course can be seen to the right.
Hydraulic Fluids
During the design of equipment that requires fluid power, many factors are considered in selecting the type of system to be used — whether hydraulic, pneumatic, or a combination of the two. Some of the factors include required speed and accuracy of operation, surrounding atmospheric conditions, economic conditions, availability of replacement fluid, required pressure level, operating temperature range, contamination possibilities, cost of transmission lines, limitations of the equipment, lubricity, safety to the operators, and expected service life of the equipment.
After the type of system has been selected, many of these same factors must be considered in selecting the fluid for the system. This chapter is devoted to hydraulic fluids. Included in it are sections on the properties and characteristics desired of hydraulic fluids; types of hydraulic fluids; hazards and safety precautions for working with, handling, and disposing of hydraulic liquids; types and control of contamination; and sampling.
Learning Objectives
When you have completed this chapter, you will be able to do the following:
- Identify the characteristics of liquid that make it desirable for use in hydraulic systems.
- Describe the properties and characteristics that must be considered in selecting a hydraulic liquid for a particular system, including related data.
- Recognize various types of hydraulic liquids and their particular characteristics and uses.
- Identify types, characteristics, and origin for various hydraulic system contaminants.
- Describe the controls and checks for various hydraulic system contaminants.
Properties
If fluidity (the physical property of a substance that enables it to flow) and incompressibility were the only properties required, any liquid not too thick might be used in a hydraulic system. However, a satisfactory liquid for a particular system must possess a number of other properties. The most important properties of hydraulic fluid and some of its characteristics are discussed in the following paragraphs.
Viscosity
Viscosity is one of the most important properties of hydraulic fluids. It is a measure of a fluid's resistance to flow. A liquid that flows easily, such as gasoline, has a low viscosity; and a liquid that flows slowly, such as tar, has a high viscosity. The viscosity of a liquid is affected by changes in temperature and pressure. As the temperature of a liquid increases, its viscosity decreases. That is, a liquid flows more easily when it is hot than when it is cold. The viscosity of a liquid increases as the pressure on the liquid increases.
A satisfactory liquid for a hydraulic system must be thick enough to give a good seal at pumps, motors, valves, and so on. These components depend on close fits for creating and maintaining pressure. Any internal leakage through these clearances results in loss of pressure, instantaneous control, and pump efficiency. Leakage losses are greater with thinner liquids (low viscosity). A liquid that is too thin will also allow rapid wearing of moving parts, or of parts that operate under heavy loads. On the other hand, if the liquid is too thick (viscosity too high), the internal friction of the liquid will cause an increase in the liquid's flow resistance through clearances of closely fitted parts, lines, and internal passages. This resistance of flow will result in pressure drops throughout the system, sluggish operation of the equipment, and an increase in power consumption.
Measurement of Viscosity
Viscosity is normally determined by measuring the time required for a fixed volume of a fluid (at a given temperature) to flow through a calibrated orifice or capillary tube. The instruments used to measure the viscosity of a liquid are known as viscometers or viscometers.
Several types of viscometers are in use today. The Saybolt viscometer, shown in Figure 3-1, measures the time required, in seconds, for 60 milliliters of the tested fluid at 100 degrees Fahrenheit (°F) to pass through a standard orifice. The time measured is used to express the fluid's viscosity, in Saybolt universal seconds or Saybolt furol seconds.
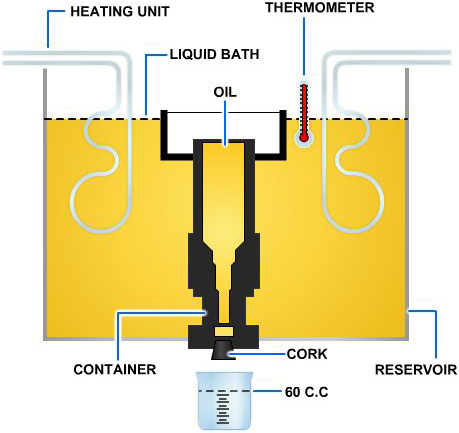
The glass capillary viscometers, shown in Figure 3-2, are examples of the second type of viscometer used. These viscometers are used to measure kinematic viscosity. Kinematic viscosity is the ratio of absolute or dynamic viscosity to density — a quantity in which no force is involved.
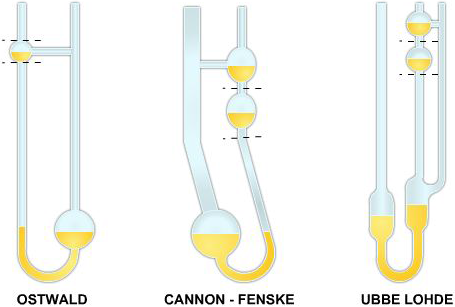
Kinematic viscosity can be obtained by dividing the dynamic viscosity of a fluid by its density:
where
ν = kinematic viscosity |
μ = absolute or dynamic viscosity |
ρ = density |
Like the Saybolt viscometer, the glass capillary measures the time in seconds required for the tested fluid to flow through the capillary. This time is multiplied by the temperature constant of the viscometer in use to provide the viscosity, expressed in centistokes.
In the International System of Units (SI-system), the theoretical unit is m2/s or commonly used stoke (St), where:
1 St = 10-4 m2/s
Because the Stoke is an impractical large unit, it is usually divided by 100 to give the unit called centistokes (cSt), where:
1 St = 100 cSt
1 cSt = 10-6 m2/s
Because the specific gravity of water at 68.4 °F (20.2 degrees Celsius (°C)) is almost 1, the kinematic viscosity of water at 68.4 °F is, for all practical purposes, 1.0 cSt.
The following formulas may be used to convert centistrokes (cSt units) to approximate Saybolt universal seconds (SUS units).
For SUS values between 32 and 100:
For SUS values greater than 100:
Although the viscometers discussed above are used in laboratories, other viscometers in the supply system are available for local use. These viscometers can be used to test the viscosity of hydraulic fluids either prior to their being added to a system or periodically after they have been in an operating system for a while.
Refer to the Naval Aircraft Carrier and Amphibious Assault Ships Metrology and Calibration (METCAL) Program Manual, NAVAIR 17-35QAL-15 for additional information on the various types of viscometers and their operation.
Viscosity Index
Viscosity index (VI) is an arbitrary measure for the change of viscosity with variations in temperature. The lower the VI, the greater the change of viscosity of the oil with temperature and vice versa. It is used to characterize viscosity changes with relation to temperature in lubricating oil. The viscosity of liquids decreases as temperature increases. The viscosity of a lubricant is closely related to its ability to reduce friction. Generally, the least viscous lubricant which still forces the two moving surfaces apart is desired. If the lubricant is too viscous, it will require a large amount of energy to move (as in honey); if it is too thin, the surfaces will come in contact and friction will increase.
An ideal oil for most purposes is one that maintains a constant viscosity throughout temperature changes. The importance of the VI can be shown easily by considering automotive lubricants. An oil with a high VI resists excessive thickening when the engine is cold, consequently promoting rapid starting and prompt circulation. It also resists excessive thinning when the motor is hot, thus providing full lubrication and preventing excessive oil consumption.
Another example of the importance of the VI is the need for a high-VI hydraulic oil for military aircraft because hydraulic control systems may be exposed to temperatures ranging from below −65 °F at high altitudes to over 100 °F on the ground. For the proper operation of the hydraulic control system, the hydraulic fluid must have a sufficiently high VI to perform its functions at the extremes of the expected temperature range.
Liquids with a high viscosity have a greater resistance to heat than low-viscosity liquids, which have been derived from the same source. The average hydraulic liquid has a relatively low viscosity. Fortunately, there is a wide choice of liquids available for use in the viscosity range required of hydraulic liquids.
The VI of an oil may be determined if its viscosity at any two temperatures is known. The American Society for Testing and Materials (ASTM) issues tables that are based on a large number of tests. These tables permit calculation of the VI from known viscosities.
Lubricating Characteristics
If motion takes place between surfaces in contact, friction tends to oppose the motion. When pressure forces the liquid of a hydraulic system between the surfaces of moving parts, the liquid spreads out into a thin film, which enables the parts to move more freely. Different liquids, including oils, vary greatly not only in their lubricating ability but also in film strength. Film strength is the capability of a liquid to resist being wiped or squeezed out from between the surfaces when spread out in an extremely thin layer. A liquid will no longer lubricate if the film breaks down because the motion of part against part wipes the metal clean of liquid.
Lubricating power varies with temperature changes; therefore, the climatic and working conditions must enter into the determination of the lubricating qualities of a liquid. Unlike viscosity, which is a physical property, the lubricating power and film strength of a liquid is directly related to its chemical nature. Lubricating qualities and film strength can be improved by the addition of certain chemical agents.
Chemical Stability
Chemical stability is another property that is exceedingly important in the selection of a hydraulic liquid. It is defined as the liquid's ability to resist oxidation and deterioration for long periods. All liquids tend to undergo unfavorable changes under severe operating conditions.
Excessive temperatures, especially extremely high temperatures, have a great effect on the life of a liquid. The temperature of the liquid in the reservoir of an operating hydraulic system does not always indicate the operating conditions throughout the system. Localized hot spots occur on bearings, on gear teeth, or at other points where the liquid under pressure is forced through small orifices. Continuous passage of the liquid through these points may produce local temperatures high enough to carbonize the liquid or turn it into sludge, yet the liquid in the reservoir may not indicate an excessively high temperature.
Liquids may break down if exposed to air, water, salt, or other impurities, especially if they are in constant motion or subjected to heat. Some metals, such as zinc, lead, brass, and copper, have undesirable chemical reactions with certain liquids.
These chemical reactions result in the formation of sludge, gums, carbon, or other deposits that clog openings, cause valves and pistons to stick or leak, and give poor lubrication to moving parts. Once a small amount of sludge or other deposits is formed, the rate of formation generally increases more rapidly. As these deposits are formed, certain changes in the physical and chemical properties of the liquid take place. The liquid usually becomes darker, the viscosity increases, and damaging acids are formed.
The extent to which changes occur in different liquids depends on the type of liquid, type of refining, and whether it has been treated to provide further resistance to oxidation. The stability of liquids can be improved by the addition of oxidation inhibitors. Inhibitors selected to improve stability must be compatible with the other required properties of the liquid.
Acidity
An ideal hydraulic liquid should be free from acids that cause corrosion of the metals in the system. Most liquids cannot be expected to remain completely noncorrosive under severe operating conditions. The degree of acidity of a liquid, when new, may be satisfactory; but after use, the liquid may tend to become corrosive as it begins to deteriorate.
Many systems are idle for long periods after operating at high temperatures. This permits moisture to condense in the system, resulting in rust formation.
Certain corrosion- and rust-preventive additives are added to hydraulic liquids. Some of these additives are effective only for a limited period. Therefore, the best procedure is to use the liquid specified for the system for the time specified by the system manufacturer and to protect the liquid and the system as much as possible from contamination by foreign matter, from abnormal temperatures, and from misuse.
Flashpoint
Flashpoint is the temperature at which a liquid gives off vapor in sufficient quantity to ignite momentarily or flash when a flame is applied. A high flashpoint is desirable for hydraulic liquids because it provides good resistance to combustion and a low degree of evaporation at normal temperatures. Required flashpoint minimums vary from 300 °F for the lightest oils to 510 °F for the heaviest oils.
Fire Point
Fire point is the temperature at which a substance gives off vapor in sufficient quantity to ignite and continue to burn when exposed to a spark or flame. Like flashpoint, a high fire point is required of desirable hydraulic liquids.
Toxicity
Toxicity is defined as the quality, state, or degree of being toxic or poisonous. Some liquids contain chemicals that are a serious toxic hazard. These toxic or poisonous chemicals may enter the body through inhalation, by absorption through the skin, or through the eyes or the mouth. The result is sickness and, in some cases, death. Manufacturers of hydraulic liquids strive to produce suitable liquids that contain no toxic chemicals. As a result, most hydraulic liquids are free of harmful chemicals. Some fire-resistant liquids are toxic, and suitable protection and care in handling must be provided.
Density and Compressibility
A fluid with a specific gravity of less than 1.0 is desired when weight is critical, although with proper system design, a fluid with a specific gravity greater than 1 can be tolerated. Where avoidance of detection by military units is desired, a fluid that sinks rather than rises to the surface of the water is desirable. Fluids having a specific gravity greater than 1.0 are desired because leaking fluid will sink, allowing the vessel with the leak to remain undetected.
Under extreme pressure, a fluid may be compressed up to 7 percent of its original volume. Highly compressible fluids produce sluggish system operation. This effect does not present a serious problem in small, low-speed operations, but it must be considered in the operating instructions.
Foaming
Foam is an emulsion of gas bubbles in the fluid. Foam in a hydraulic system results from compressed gases in the hydraulic fluid. A fluid under high pressure can contain a large volume of air bubbles. When this fluid is depressurized, as when it reaches the reservoir, the gas bubbles in the fluid expand and produce foam. Any amount of foaming may cause pump cavitation and produce poor system response and spongy control. Therefore, defoaming agents are often added to fluids to prevent foaming. Minimizing air in fluid systems is discussed later in this chapter.
Cleanliness
Cleanliness in hydraulic systems has received considerable attention recently. Some hydraulic systems, such as aerospace hydraulic systems, are extremely sensitive to contamination. Fluid cleanliness is of primary importance because contaminants can cause component malfunction, prevent proper valve seating, cause wear in components, and increase the response time of servo valves. Fluid contaminants are discussed later in this chapter.
The inside of a hydraulic system can only be kept as clean as the fluid added to it. Initial fluid cleanliness can be achieved by observing stringent cleanliness requirements (discussed later in this chapter) or by filtering all fluid added to the system.
Types of Hydraulic Fluids
Many liquids have been tested for use in hydraulic systems. Currently, liquids being used include mineral oil, water, phosphate ester, water-based ethylene glycol compounds, and silicone fluids. The three most common types of hydraulic liquids are petroleum-based, synthetic fire-resistant, and water-based fire-resistant.
Petroleum-Based Fluids
The most common hydraulic fluids used in shipboard systems are the petroleum-based oils. These fluids contain additives to protect the fluid from oxidation (antioxidant), to protect system metals from corrosion (anticorrosion), to reduce tendency of the fluid to foam (foam suppressant), and to improve viscosity.
Petroleum-based fluids are used in surface ships' electrohydraulic steering and deck machinery systems; submarines' hydraulic systems; and aircraft automatic pilots, shock absorbers, brakes, control mechanisms, and other hydraulic systems using seal materials compatible with petroleum-based fluids.
Synthetic Fire-Resistant Fluids
Petroleum-based oils contain most of the desired properties of a hydraulic liquid. However, they are flammable under normal conditions and can become explosive when subjected to high pressures and a source of flame or high temperatures. Nonflammable synthetic liquids have been developed for use in hydraulic systems where fire hazards exist.
Phosphate Ester Fire-Resistant Fluid
Phosphate ester fire-resistant fluid for shipboard use is covered by specification MIL-H-19457. Tertiary butylated triphenyl phosphate fluids per MIL-H-19457 have been used in aircraft elevators and other surface ship hydraulic systems where a fire-resistant fluid is required. These fluids will be delivered in containers marked MIL-H-19457C or a later specification revision. Phosphate ester in containers marked by a brand name without a specification identification must not be used in shipboard systems because they may contain toxic chemicals.
These fluids will burn if sufficient heat and flame are applied, but they do not support combustion. Drawbacks of phosphate ester fluids are that they will attack and loosen commonly used paints and adhesives, deteriorate many types of insulations used in electrical cables, and deteriorate many gasket and seal materials. Therefore, specific materials are used to manufacture gaskets and seals for systems in which phosphate ester fluids are used. Naval Ships' Technical Manual (NSTM), chapter 556, specifies paints to be used on exterior surfaces of hydraulic systems and components in which phosphate ester fluid is used and on ship structure and decks in the immediate vicinity of this equipment. NSTM, chapter 078, specifies gasket and seal materials used. The Aviation Hydraulics Manual, NAVAIR 01-1A-17 also contains a list of materials resistant to phosphate ester fluids.
Trade names for phosphate ester fluids that do not conform to MIL-H-19457 include Pydraul, Skydrol, and Fyre Safe.
Phosphate Ester Fluid Safety
As a maintenance person, operator, supervisor, or crew member of a ship, squadron, or naval shore installation, you must understand the hazards associated with hydraulic fluids to which you may be exposed.
Phosphate ester fluid conforming to specification MIL-H-19457 is used in aircraft elevators, ballast valve operating systems, and replenishment-at-sea systems. This type of fluid contains a controlled amount of neurotoxic material. Because of the neurotoxic effects that can result from ingestion, skin absorption, or inhalation of these fluids, be sure to use the following precautions:
- Avoid contact with the fluids by wearing protective clothing.
- Use chemical goggles or face shields to protect your eyes.
- If you are expected to work in an atmosphere containing a fine mist or spray, wear a continuous-flow airline respirator.
- Thoroughly clean skin areas contaminated by this fluid with soap and water.
- If you get any fluid in your eyes, flush them with running water for at least 15 minutes and seek medical attention.
If you come in contact with MIL-H-19457 fluid, report the contact when you seek medical aid and whenever you have a routine medical examination.
NSTM, chapter 556, contains a list of protective clothing, along with national stock numbers (NSNs), for use with fluids conforming to MIL-H-19457. It also contains procedures for repair work and for low-level leakage and massive spills cleanup.
Phosphate Ester Fluid Disposal
Waste fluids and refuse (rags and other materials) must not be dumped at sea. Fluid should be placed in bung-type drums. Rags and other materials should be placed in open-top drums for shore disposal. These drums should be marked with a warning label stating their content, safety precautions, and disposal instructions. Refer to NSTM chapter 556 and OPNAVINST 5090.1, Environmental Readiness Program Manual for detailed instructions on phosphate ester fluids disposal.
Synthetic Fire-Resistant Fluids (Silicone)
Synthetic fire-resistant fluids are frequently used for hydraulic systems that require fire resistance but have only marginal requirements for other chemical or physical properties common to hydraulic fluids. Silicone fluids do not have the detrimental characteristics of phosphate ester fluids, nor do they provide the corrosion protection and lubrication of phosphate ester fluids, but they are excellent for fire protection. Silicone fluid conforming to MIL-S-81087 is used in the missile holddown and lockout system aboard submarines.
Lightweight Synthetic Fire-Resistant Fluids
In applications where weight is critical, lightweight synthetic fluid is used in hydraulic systems. MIL-H-83282 is a synthetic, fire-resistant hydraulic fluid used in military aircraft and hydrofoils where the requirement to minimize weight dictates the use of a low-viscosity fluid. It is also the most commonly used fluid in aviation support equipment. NAVAIR 01-1A-17 contains additional information on fluids conforming to specification MIL-H-83282.
Water-Based Fire-Resistant Fluids
The most widely used water-based hydraulic fluids may be classified as water-glycol mixtures and water-synthetic base mixtures. The waterglycol mixture contains additives to protect it from oxidation, corrosion, and biological growth and to enhance its load-carrying capacity.
Fire resistance of the water mixture fluids depends on the vaporization and smothering effect of steam generated from the water. The water in water-based fluids is constantly being driven off while the system is operating. Therefore, frequent checks to maintain the correct ratio of water are important.
The water-based fluid used in aircraft handling machinery (catapults), catapult retracting engines, and jet blast deflectors conforms to MIL-H-22072.
The safety precautions outlined for phosphate ester fluid and the disposal of phosphate ester fluid also apply to water-based fluid conforming to MIL-H-22072.
Contamination
Hydraulic fluid contamination may be described as any foreign material or substance whose presence in the fluid is capable of adversely affecting system performance or reliability. It may assume many different forms, including liquids, gases, and solid matter of various compositions, sizes, and shapes. Solid matter is the type most often found in hydraulic systems and is generally referred to as particulate contamination. Contamination is always present to some degree, even in new, unused fluid, but must be kept below a level that will adversely affect system operation. Hydraulic contamination control consists of requirements, techniques, and practices necessary to minimize and control fluid contamination.
Classification
Many types of contaminants are harmful to hydraulic systems and liquids. These contaminants may be divided into two different classes — particulate and fluid.
Particulate Contamination
This class of contaminants includes organic, metallic solid, and inorganic solid contaminants. These contaminants are discussed in the following paragraphs.
Organic Contamination
Organic solids or semisolids found in hydraulic systems are produced by wear, oxidation, or polymerization. Minute particles of O-rings, seals, gaskets, and hoses are present due to wear or chemical reactions. Synthetic products, such as neoprene, silicones, and hypalon, though resistant to chemical reaction with hydraulic fluids, produce small wear particles. Oxidation of hydraulic fluids increases with pressure and temperature, although antioxidants are blended into hydraulic fluids to minimize such oxidation. The ability of a hydraulic fluid to resist oxidation or polymerization in service is defined as its oxidation stability. Oxidation products appear as organic acids, asphaltics, gums, and varnishes. These products combine with particles in the hydraulic fluid to form sludge. Some oxidation products are oil soluble and cause the hydraulic fluid to increase in viscosity; other oxidation products are not oil soluble and form sediment.
Metallic Solid Contamination
Metallic contaminants are almost always present in a hydraulic system and will range in size from microscopic particles to particles readily visible to the naked eye. These particles are the result of wearing and scoring of bare metal parts and plating materials, such as silver and chromium. Although practically all metals commonly used for parts fabrication and plating may be found in hydraulic fluids, the major metallic materials found are ferrous, aluminum, and chromium particles. Because of their continuous high-speed internal movement, hydraulic pumps usually contribute most of the metallic particulate contamination present in hydraulic systems. Metal particles are also produced by other hydraulic system components, such as valves and actuators, due to body wear and the chipping and wearing away of small pieces of metal plating materials.
Inorganic Solid Contamination
This contaminant group includes dust, paint particles, dirt, and silicates. Glass particles from glass bead peening and blasting may also be found as contaminants. Glass particles are very undesirable contaminants due to their abrasive effect on synthetic rubber seals and the very fine surfaces of critical moving parts. Atmospheric dust, dirt, paint particles, and other materials are often drawn into hydraulic systems from external sources. For example, the wet piston shaft of a hydraulic actuator may draw some of these foreign materials into the cylinder past the wiper and dynamic seals, and the contaminant materials are then dispersed in the hydraulic fluid. Contaminants may also enter the hydraulic fluid during maintenance when tubing, hoses, fittings, and components are disconnected or replaced. It is therefore important that all exposed fluid ports be sealed with approved protective closures to minimize such contamination.
Fluid Contamination
Air, water, solvent, and other foreign fluids are in the class of fluid contaminants.
Air Contamination
Hydraulic fluids are adversely affected by dissolved, entrained, or free air. Air may be introduced through improper maintenance or as a result of system design. Any maintenance operation that involves breaking into the hydraulic system, such as disconnecting or removing a line or component, will invariably result in some air being introduced into the system. This source of air can and must be minimized by prefilling replacement components with new filtered fluid prior to their installation. Failing to prefill a filter element bowl with fluid is a good example of how air can be introduced into the system. Although prefilling will minimize introduction of air, it is still important to vent the system where venting is possible.
Most hydraulic systems have built-in sources of air. Leaky seals in gas-pressurized accumulators and reservoirs can feed gas into a system faster than it can be removed, even with the best of maintenance. Another lesser known but major source of air is air that is sucked into the system past actuator piston rod seals. This usually occurs when the piston rod is stroked by some external means while the actuator itself is not pressurized.
Water Contamination
Water is a serious contaminant of hydraulic systems. Hydraulic fluids are adversely affected by dissolved, emulsified, or free water. Water contamination may result in the formation of ice, which impedes the operation of valves, actuators, and other moving parts. Water can also cause the formation of oxidation products and corrosion of metallic surfaces.
Solvent Contamination
Solvent contamination is a special form of foreign-fluid contamination in which the original contaminating substance is a chlorinated solvent. Chlorinated solvents or their residues may, when introduced into a hydraulic system, react with any water present to form highly corrosive acids.
Chlorinated solvents, when allowed to combine with minute amounts of water often found in operating hydraulic systems, change chemically into hydrochloric acids. These acids then attack internal metallic surfaces in the system, particularly those that are ferrous, and produce a severe rustlike corrosion. NAVAIR 01-1A-17 and NSTM, chapter 556, contain tables of solvents for use in hydraulic maintenance.
Foreign-Fluids Contamination
Hydraulic systems can be seriously contaminated by foreign fluids other than water and chlorinated solvents. This type of contamination is generally a result of lube oil, engine fuel, or incorrect hydraulic fluid being introduced inadvertently into the system during servicing. The effects of such contamination depend on the contaminant, the amount in the system, and how long it has been present.
It is extremely important that the different types of hydraulic fluids are not mixed in one system. If different type hydraulic fluids are mixed, the characteristics of the fluid required for a specific purpose are lost. Mixing the different types of fluids usually will result in a heavy, gummy deposit that will clog passages and require a major cleaning. In addition, seals and packing installed for use with one fluid usually are not compatible with other fluids, and damage to the seals will result.
Origin of Contamination
Recall that contaminants are produced from wear and chemical reactions, introduced by improper maintenance, and inadvertently introduced during servicing. These methods of contaminant introduction fall into one of the four major areas of contaminant origin.
Particles Originally Contained in the System
These particles originate during the fabrication and storage of system components. Weld spatter and slag may remain in welded system components, especially in reservoirs and pipe assemblies. The presence is minimized by proper design. For example, seam-welded overlapping joints are preferred, and arc welding of open sections is usually avoided. Hidden passages in valve bodies, inaccessible to sand blasting or other methods of cleaning, are the main source of introduction of core sand. Even the most carefully designed and cleaned casting will almost invariably free some sand particles under the action of hydraulic pressure. Rubber hose assemblies always contain some loose particles. Most of these particles can be removed by flushing the hose before installation; however, some particles withstand cleaning and are freed later by the action of hydraulic pressure.
Particles of lint from cleaning rags can cause abrasive damage in hydraulic systems, especially to closely fitted moving parts. In addition, lint in a hydraulic system packs easily into clearances between packing and contacting surfaces, leading to component leakage and decreased efficiency. Lint also helps clog filters prematurely. The use of the proper wiping materials will reduce or eliminate lint contamination. The wiping materials to be used for a given application will be determined by:
- Substances being wiped or absorbed
- The amount of absorbency required
- The required degree of cleanliness
These wiping materials are categorized for contamination control by the degree of lint or debris that they may deposit during use. For internal hydraulic repairs, this factor itself will determine the choice of wiping material. NAVAIR 01-1A-17 and NSTM, chapter 556, provide information on low-lint wiping cloths.
Rust or corrosion initially present in a hydraulic system can usually be traced to improper storage of materials and component parts. Particles can range in size from large flakes to abrasives of microscopic dimensions. Proper preservation of stored parts is helpful in eliminating corrosion.
Particles Introduced from Outside Sources
Particles can be introduced into hydraulic systems at points where either the liquid or certain working parts of the system (for example, piston rods) are at least in temporary contact with the atmosphere.
The most common contaminant introduction areas are at the refill and breather openings, cylinder rod packings, and open lines where components are removed for repair or replacement. Contamination arising from carelessness during servicing operations is minimized by the use of filters in the system fill lines and finger strainers in the filler adapter of hydraulic reservoirs. Hydraulic cylinder piston rods incorporate wiper rings and dust seals to prevent the dust that settles on the piston rod during its outward stroke from entering the system when the piston rod retracts. Caps and plugs are available and should be used to seal off the open lines when a component is removed for repair or replacement.
Particles Created Within the System During Operation
Contaminants created during system operation are of two general types — mechanical and chemical. Particles of a mechanical nature are formed by the wearing of parts in frictional contact, such as pumps, cylinders, and packing gland components. These wear particles can vary from large chunks of packings down to steel shavings that are too small to be trapped by filters.
The major source of chemical contaminants in hydraulic liquid is oxidation. These contaminants are formed under high pressure and temperatures and are promoted by the chemical action of water and air and of metals such as copper and iron oxides. Liquid-oxidation products appear initially as organic acids, asphaltines, gums, and varnishes — sometimes combined with dust particles as sludge. Liquid-soluble oxidation products tend to increase liquid viscosity, while insoluble types separate and form sediments, especially on colder elements such as heat exchanger coils.
Liquids containing antioxidants have little tendency to form gums and sludge under normal operating conditions. However, as the temperature increases, resistance to oxidation diminishes. Hydraulic liquids that have been subjected to excessively high temperatures (above 250 °F for most liquids) will break down, leaving minute particles of asphaltines suspended in the liquids. The liquid changes to brown in color and is referred to as decomposed liquid. This process explains the importance of keeping the hydraulic liquid temperature below specific levels.
The second contaminant-producing chemical action in hydraulic liquids is one that permits these liquids to react with certain types of rubber. This reaction causes structural changes in the rubber, turning it brittle and finally causing its complete disintegration. For this reason, the compatibility of system liquid with seals and hose material is a very important factor.
Particles Introduced by Foreign Liquids
One of the most common foreign-fluid contaminants is water, especially in hydraulic systems that require petroleum-based liquids. Water, which enters even the most carefully designed system by condensation of atmospheric moisture, normally settles to the bottom of the reservoir. Oil movement in the reservoir disperses the water into fine droplets, and agitation of the liquid in the pump and in high-speed passages forms an oil-water-air emulsion. This emulsion normally separates during the rest period in the system reservoir; but when fine dust and corrosion particles are present, the emulsion is chemically changed by high pressures into sludge. The damaging action of sludge explains the need for effective filtration, as well as the need for water separation qualities in hydraulic liquids.
Contamination Control
Maintaining hydraulic fluid within allowable contamination limits for both water and particulate matter is crucial to the care and protection of hydraulic equipment.
Filters will provide adequate control of the particular contamination problem during all normal hydraulic system operations if the filtration system is installed properly and filter maintenance is performed properly. Filter maintenance includes changing elements at proper intervals. Control of the size and amount of contamination entering the system from any other source is the responsibility of the personnel who service and maintain the equipment. During installation, maintenance, and repair of hydraulic equipment, the retention of cleanliness of the system is of paramount importance for subsequent satisfactory performance.
Adhere to the following maintenance and servicing procedures at all times to provide proper contamination control:
- Keep all tools and the work area (workbenches and test equipment) in a clean, dirt-free condition.
-
Ensure a suitable container is always provided to receive the hydraulic liquid that is spilled during component removal or disassembly.
NOTE
After draining liquid from these systems for reuse, store it in a clean and suitable container. Strain and/or filter the liquid when returning it to the system reservoir.
- Before disconnecting hydraulic lines or fittings, clean the affected area with an approved dry-cleaning solvent.
- Cap or plug all hydraulic lines and fittings immediately after disconnection.
- Before assembling any hydraulic components, wash their parts with an approved dry-cleaning solvent.
-
After cleaning the parts in dry-cleaning solvent, dry them thoroughly with clean, low-lint cloths and lubricate with the recommended preservative or hydraulic liquid before assembling.
NOTE
Only use clean, low-lint type I or II cloths as appropriate to wipe or dry component parts.
- Replace all packings and gaskets during the assembly procedures.
- Connect all parts with care to avoid stripping metal slivers from threaded areas. Install and torque all fittings and lines according to applicable technical instructions.
- Keep all hydraulic servicing equipment clean and in good operating condition.
Some hydraulic fluid specifications, such as MIL-H-6083, MIL-H-46170, and MIL-H-83282, contain particle contamination limits that are so low that the products are packaged under clean room conditions. Very slight amounts of dirt, rust, and metal particles will cause them to fail the specification limit for contamination. Because these fluids are usually all packaged in hermetically sealed containers, the act of opening a container may allow more contaminants into the fluid than the specification allows. Therefore, take extreme care in the handling of these fluids. In opening the container for use, observation, or tests, it is extremely important to open and handle the can in a clean environment. Flush the area of the container to be opened with filtered solvent (petroleum ether or isopropyl alcohol), and thoroughly rinse the device used for opening the container with filtered solvent. After opening the container, pour a small amount of the material from the container and disposed of it before pouring the sample for analysis. Once you have opened a container, if the contents are not totally used, discard the unused portion. Because the level of contamination of a system containing these fluids must be kept low, perform maintenance on the system's components in a clean environment commonly known as a controlled environment work center. Refer to Aviation Hydraulics Manual, NAVAIR 01-1A-17, for specific information about the controlled environment work center.
Hydraulic Fluid Sampling
The condition of a hydraulic system, as well as its probable future performance, can best be determined by analyzing the operating fluid. Of particular interest are any changes in the physical and chemical properties of the fluid and excessive particulate or water contamination, either of which indicates impending trouble. Excessive particulate contamination of the fluid indicates that the filters are not keeping the system clean. This impediment can result from improper filter maintenance, inadequate filters, or excessive ongoing corrosion and wear.
Sample operating equipment according to instructions given in the operating and maintenance manual for the particular equipment or as directed by the Maintenance Requirement Cards (MRCs).
- Take all samples from circulating systems, or immediately upon shutdown, while the hydraulic fluid is within 5 °C (9 °F) of normal system operating temperature. Systems not up to temperature may provide nonrepresentative samples of system dirt and water content. Discard the first oil coming from the sampling point because it can be dirty and does not represent the system. Either avoid such samples or indicate the status on the analysis report. As a general rule, a volume of oil equivalent to one to two times the volume of oil contained in the sampling line and valve should be drained before the sample is taken.
- Ideally, take the sample from a valve installed specifically for sampling. When sampling valves are not installed, avoid taking samples from locations where sediment or water can collect, such as dead ends of piping, tank drains, and low points of large pipes and filter bowls, if possible. If taking samples from pipe drains, drain sufficient fluid before taking the sample to ensure that the sample actually represents the system. Do not take samples from the tops of reservoirs or other locations where the contamination levels are normally low.
-
Unless otherwise specified, take a minimum of one sample for each system located wholly within one compartment. For ships' systems extending into two or more compartments, a second sample is required. An exception to this requirement is submarine external hydraulic systems, which require only one sample. Label original sample points, and use the same sample points for successive sampling. If possible, select the following sampling locations:
- A location that provides a sample representative of fluid being supplied to system components
- A return line as close to the supply tank as practical but upstream of any return line filter
- For systems requiring a second sample, a location as far from the pump as practical
Operation of the sampling point should not introduce any significant amount of external contaminants into the collected fluid. For additional information on hydraulic fluid sampling, refer to NAVAIR 01-1A-17.
Most fluid samples are submitted to shore laboratories for analysis. Refer to NAVAIR 17-15-50-1, NSTM chapter 556, and NSTM 226 for additional information on collection, labeling, and shipping samples.
PDH Classroom offers a continuing education course based on this hydraulic fluids reference page. This course can be used to fulfill PDH credit requirements for maintaining your PE license.
Now that you've read this reference page, earn credit for it!