Chapter 4: Pumps
This page provides the chapter on hydraulic pumps from the U.S. Navy's fluid power training course, NAVEDTRA 14105A, "Fluid Power," Naval Education and Training Professional Development and Technology Center, July 2015.
Other related chapters from the Navy's fluid power training course can be seen to the right.
Pumps
Pumps are used for some essential services in the Navy. Pumps supply water to the boilers, draw condensation from the condensers, supply sea water to the firemain, circulate cooling water for coolers and condensers, pump out bilges, transfer fuel, supply water to the distilling plants, and serve many other purposes. Although the pumps discussed in this chapter are used primarily in hydraulic systems, the principles of operation apply as well to the pumps used in other systems.
Learning Objectives
When you have completed this chapter, you will be able to do the following:
- Explain the functions, operating characteristics, and related data pertinent to hydraulic pumps.
- Identify operating principles and construction features of rotary pumps.
- Recognize functions and principles of operation of various types of reciprocating pumps.
- Describe the construction features of various types of reciprocating pumps.
Purpose
The purpose of a hydraulic pump is to supply a flow of fluid to a hydraulic system. The pump does not create system pressure, since pressure can be created only by a resistance to the flow. As the pump provides flow, it transmits a force to the fluid. As the fluid flow encounters resistance, this force is changed into a pressure. Resistance to flow is the result of a restriction or obstruction in the path of the flow. This restriction is normally the work accomplished by the hydraulic system, but can also be restrictions of lines, fittings, and valves within the system. Thus, the pressure is controlled by the load imposed on the system or the action of a pressure-regulating device.
Operation
A pump must have a continuous supply of fluid available to the inlet port to supply fluid to the system. As the pump forces fluid through the outlet port, a partial vacuum or low-pressure area is created at the inlet port. When the pressure at the inlet port of the pump is lower than the local atmospheric pressure, atmospheric pressure acting on the fluid in the reservoir forces the fluid into the pump's inlet. If the pump is located at a level lower than the reservoir, the force of gravity supplements atmospheric pressure on the reservoir. Aircraft and missiles that operate at high altitudes are equipped with pressurized hydraulic reservoirs to compensate for low atmospheric pressure encountered at high altitudes.
Performance
Pumps are normally rated by their volumetric output and pressure. Volumetric output is the amount of fluid a pump can deliver to its outlet port in a certain period of time at a given speed. Volumetric output is usually expressed in gallons per minute. Since changes in pump speed affect volumetric output, some pumps are rated by their displacement. Pump displacement is the amount of fluid the pump can deliver per cycle. Since most pumps use a rotary drive, displacement is usually expressed in terms of cubic inches per revolution.
As a pump does not create pressure, however, pressure develops by the restrictions in the system affecting the volumetric output of the pump. As the system pressure increases, the volumetric output decreases. This drop in volumetric output is the result of an increase in the amount of internal leakage from the outlet side to the inlet side of the pump. This leakage is referred to as pump slippage and is a factor that must be considered in all pumps. This explains why most pumps are rated in terms of volumetric output at a given pressure.
Classification of Pumps
Many different methods are used to classify pumps. Terms such as positive-displacement, nonpositive-displacement, fixed-displacement, variable-displacement, fixed delivery, variable delivery, constant volume, and others are used to describe pumps. The first two of these terms describe the fundamental division of pumps; that is, all pumps are either positive-displacement or nonpositive-displacement.
Basically, pumps that discharge liquid in a continuous flow are referred to as nonpositive-displacement, and those that discharge volumes separated by a period of no discharge are referred to as positive-displacement.
Nonpositive-displacement pumps impart velocity to the liquid resulting in a pressure at the discharge (pressure is created and flow is the result).
Positive-displacement pumps capture confined amounts of liquid and transfer it from the suction to the discharge (flow is created and pressure is the result).
Nonpositive-Displacement Pumps
The nonpositive-displacement pump can be classified as centrifugal or propeller.
Centrifugal
The centrifugal pump is a nonpositive-displacement pump which delivers a continuous flow produced by a rotating impeller. Centrifugal pumps are widely used aboard ship for pumping nonviscous liquids. In the engine room you will find several important centrifugal pumps: the feed booster pump, the fire and flushing pump, condensate pumps, auxiliary circulating pumps, and the main feed pump. They have several advantages over reciprocating pumps; they are simpler, more compact, lighter, and easily adapted to a high-speed prime mover. Centrifugal pumps also have disadvantages; they have poor suction lift characteristics and they are sensitive to variations in head and speed.
The centrifugal pump uses the throwing force of a rapidly revolving impeller. The liquid is pulled in at the center or eye of the impeller and is discharged at its outer rim. By the time the liquid reaches the outer rim of the impeller, it has acquired a considerable velocity (kinetic energy). The liquid is then slowed down by being led through a volute or through a series of diffusing passages. As the velocity of the liquid decreases, its pressure increases and thus its kinetic energy is transformed into potential energy.
A centrifugal pump does not provide a positive seal against slippage; therefore, the output of the pump varies as system pressure varies. In other words, the volume of fluid delivered for each cycle depends on the resistance to the flow. This type of pump produces a force on the fluid that is constant for each particular speed of the pump. Resistance in the discharge line produces a force in a direction opposite the direction of the force produced by the pump. When these forces are equal, the fluid is in a state of equilibrium and does not flow.
Types of Centrifugal Pumps
There are many different types of centrifugal pumps, but the two which are most likely encountered aboard ship are the volute pump and the volute turbine, or diffuser pump.
Volute Pump
In the volute pump shown in Figure 4-1, the impeller discharges into a volute. As the liquid passes through the volute (a gradually widening spiral channel in the pump casing) and into the discharge nozzle, a great part of its kinetic energy is converted into potential energy.
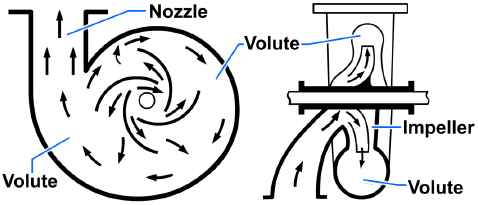
Diffuser Pump
In the diffuser pump shown in Figure 4-2, the liquid leaving the impeller is first slowed down by the stationary diffuser vanes which surround the impeller. The liquid is forced through gradually widening passages in the diffuser ring (not shown) and into the volute. Since both the diffuser vanes and the volute reduce the velocity of the liquid, there is an almost complete conversion of kinetic energy to potential energy.
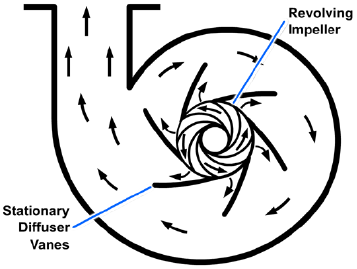
Propeller Pumps
A propeller pump is another type of nonpositive-displacement pump. This pump is used primarily where there is a large volume of liquid with a relatively low total head requirement. This pump is usually limited to where the total head does not exceed 40 to 60 feet.
The chief use of the propeller pump is for the main condenser circulating pump. In most ships this has an emergency suction for pumping out the engine room.
The main condenser circulating pump is of the vertical propeller type. The pump unit consists of three major parts: the propeller, together with its bearings and shaft; the pump casing; and the driving unit, which may be an auxiliary steam turbine or electric motor.
The propeller is a multibladed screw propeller having a large pitch. The blades are thick at the roots and flare out toward the tips. The blades and hubs are cast or forged in one piece and are then machined and balanced. The lower shaft bearing is a water-lubricated sleeve bearing. The shaft packing gland prevents excessive leakage of water between the casing and the shaft.
If the discharge valve of a nonpositive-displacement pump is completely shut, the discharge pressure will increase to the maximum for that particular pump at a specific speed. Nothing more will happen except that the pump will churn the fluid and produce heat.
Positive-Displacement Pumps
The positive-displacement pump can be classified as:
- Reciprocating pumps - piston, plunger, and diaphragm
- Variable-stroke pumps
- Rotary pumps - gear, lobe, screw, and vane
A positive-displacement pump is one in which a definite volume of liquid is delivered for each cycle of pump operation. Positive-displacement pumps use two opposing, rotating elements to displace liquid from the suction side of the pump to the discharge side of the pump. As the elements rotate, the chamber formed between the rotors, housing, and cover collects the liquid on the inlet side of the pump and carries the liquid to the discharge side of the pump. Positive-displacement pumps are used for low flow and high-pressure applications.
Positive-displacement pumps sometimes do not pump the full displacement for which they are rated because of slippage. To allow a positive pump's rotors to rotate, small clearances must be maintained between the rotors and housing. The liquid that slips by will partially fill the inlet cavity. This amount of liquid must be repumped, preventing the pump from reaching its full rated capacity and decreasing its volumetric efficiency.
Positive-displacement pumps physically displace the fluid; therefore, shutting a valve downstream of a positive-displacement pump will result in a continual buildup in pressure resulting in severe damage to the pipeline or pump.
Positive-displacement pumps are further classified as fixed-displacement or variable-displacement. The fixed-displacement pump delivers the same amount of fluid on each cycle.
The variable-displacement pump is constructed so that the displacement per cycle can be varied. The displacement is varied through the use of an internal controlling device.
Design Classifications
Pumps may also be classified according to the specific design used to create the flow of fluid. Practically all hydraulic pumps fall within three design classifications − centrifugal, rotary, and reciprocating. The use of centrifugal pumps in hydraulics is limited and will not be discussed in this text.
Rotary Pumps
All rotary pumps have rotating parts which trap the fluid at the inlet (suction) port and force it through the discharge port into the system. Gears, screws, lobes, and vanes are commonly used to move the fluid. Rotary pumps are positive-displacement of the fixed-displacement type. The rotary pump tree is illustrated in Figure 4-3.
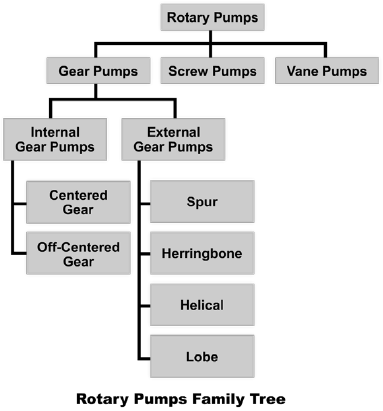
Rotary pumps (Figure 4-4 through Figure 4-7) are designed with very small clearances between rotating parts and stationary parts to minimize slippage from the discharge side back to the suction side. These types of pumps are designed to operate at relatively moderate speeds. Operating at high speeds causes erosion and excessive wear which results in increased clearances.
There are numerous types of rotary pumps and various methods of classification. They may be classified by the shaft position — either vertically or horizontally mounted; the type of drive — electric motor, gasoline engine, and so forth; their manufacturer's name; or their service application. However, classification of rotary pumps is generally made according to the type of rotating element. A few of the most common types of rotary pumps are discussed in the following paragraphs.

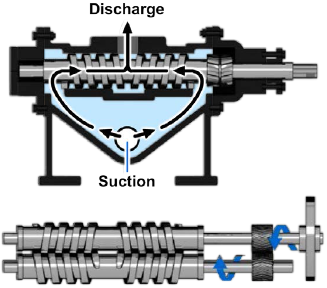
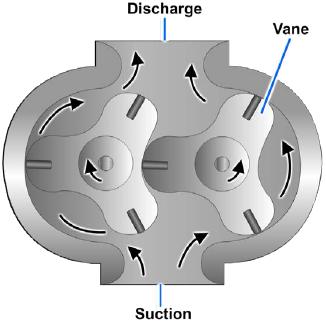
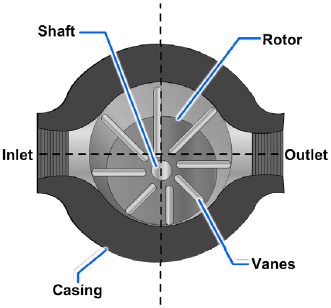
Internal Gear Pumps
Internal gear pumps deliver fluid between the gear teeth from the inlet to outlet ports. The outer gear (rotor) drives the inner or idler gear on a stationary pin. The gears create voids as they come out of mesh and fluid flows into the cavities. As the gears come back into mesh, the volume is reduced and the liquid is forced out of the discharge port. The crescent prevents liquid from flowing backwards from the outlet to the inlet port. Internal gear pumps may be either centered or off-centered. Internal gear pumps may be further divided into those with a crescent and those with no crescent.
Off-Centered Internal Gear Pump
This pump is illustrated in Figure 4-8. The drive gear is attached directly to the drive shaft of the pump and is placed off-center in relation to the internal gear. The two gears mesh on one side of the pump, between the suction (inlet) and discharge ports. On the opposite side of the chamber, a crescent-shaped form fitted to a close tolerance fills the space between the two gears.
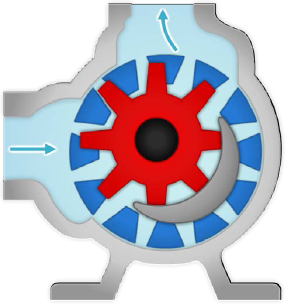
The rotation of the center gear by the drive shaft causes the outside gear to rotate, since the two are meshed. Everything in the chamber rotates except the crescent. This rotation causes liquid to be trapped in the gear spaces as they pass the crescent. The liquid is carried from the suction port to the discharge port where it is forced out of the pump by the meshing of the gears. The size of the crescent that separates the internal and external gears determines the volume delivery of the pump. A small crescent allows more volume of liquid per revolution than a larger crescent.
Internal Gear Pump with No Crescent
In contrast to the internal gear pump with a crescent, the internal gear pump without crescent consists of a gear within a gear. This pump consists of a pair of gear-shaped elements — one within the other — located in the pump chamber. The inner gear is connected to the drive shaft of the power source.
The operation of this type of internal gear pump is illustrated in Figure 4-9. The tooth design of each gear is related to that of the other in such a way that each tooth of the inner gear is always in sliding contact with the surface of the outer gear. Each tooth of the inner gear meshes with the outer gear at just one point during each revolution. As the gears continue to rotate in a clockwise direction, the inner gear teeth approach and mesh with the outer gear teeth. Note that the inner gear has one less tooth than the outer gear. As a result, the outer gear rotates at just six-sevenths the speed of the inner gear. For example, if the inner gear rotates at 1,400 revolutions per minute (rpm), the outer gear rotates at 1,200 rpm.
At one side of the point of mesh, pockets of increasing size are formed as the gears rotate; simultaneously, the pockets decrease in size on the other side. The pockets on the right-hand side of the drawings increase in size as you move down the illustration, while those on the left-hand side decrease in size. The motion of the gears draws fluid in on one side of the pump and pushes it out of the other side.
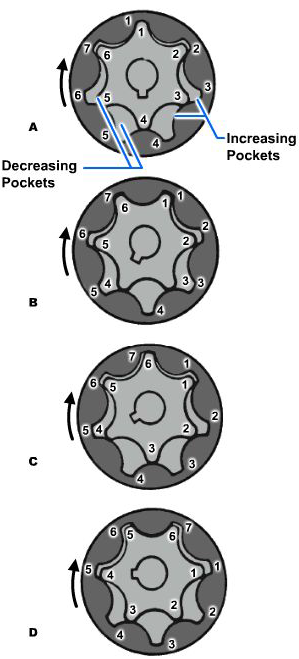
Internal Gear Pump Operation
The operation of this type of internal gear pump is illustrated in Figure 4-10. To simplify the explanation, the teeth of the inner gear and the spaces between the teeth of the outer gear are numbered. Note that the inner gear has one less tooth than the outer gear. The tooth form of each gear is related to that of the other in such a way that each tooth of the inner gear is always in sliding contact with the surface of the outer gear. Each tooth of the inner gear meshes with the outer gear at just one point during each revolution. In the illustration, this point is at the X. In view A, tooth 1 of the inner gear is meshed with space 1 of the outer gear. As the gears continue to rotate in a clockwise direction and the teeth approach point X, tooth 6 of the inner gear will mesh with space 7 of the outer gear, tooth 5 with space 6, and so on. During this revolution, tooth 1 will mesh with space 2; and during the following revolution, tooth 1 will mesh with space 3. As a result, the outer gear will rotate at just six-sevenths the speed of the inner gear.
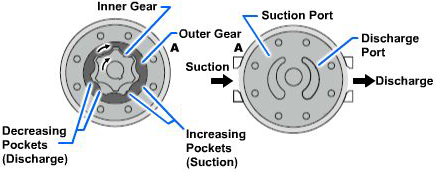
At one side of the point of mesh, pockets of increasing size are formed as the gears rotate, while on the other side the pockets decrease in size. In Figure 4-10, the pockets on the right-hand side of the drawings are increasing in size toward the bottom of the illustration, while those on the left-hand side are decreasing in size toward the top of the illustration. The intake side of the pump would therefore be on the right and the discharge side on the left.
External Gear Pumps
External gear pumps (Figure 4-11) are similar to internal gear pumps in that two gears come into and out of mesh to produce flow. In the external gear pump, one gear (drive gear) is driven by a motor and in turn drives the other gear (driven gear). As the gears mesh, the fluid, which is trapped in the gear teeth spaces between the housing and the outside of the gears, are transferred from the suction side of the pump to the discharge side. As the gears come out of mesh, they create expanding volume on the inlet side of the pump.

Because the gears are supported on both sides, external gear pumps are quiet-running and are routinely used for high-pressure applications such as hydraulic applications. With no overhung bearing loads, the rotor shaft can't deflect and cause premature wear.
Spur Tooth Gear Pump
The spur gear pump (Figure 4-12) consists of two meshed gears which revolve in a housing. The drive gear in the illustration is turned by a drive shaft which is attached to the power source. The clearances between the gear teeth as they mesh and the pump housing are very small.
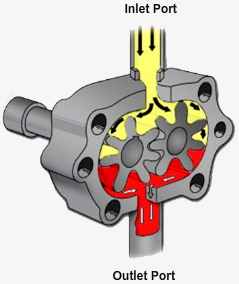
Herringbone Gear Pump
The herringbone gear pump (Figure 4-13) is a modification of the spur gear pump. A herringbone gear is composed of two helixes spiraling in different directions from the center of the gear. The liquid is pumped in the same manner as in the spur gear pump; however, the herringbone pump has two sets of teeth (double helical) set in a V-shape. Each set of teeth begins its fluid discharge phase before the previous set of teeth has completed its discharge phase. This overlapping of teeth and the relatively larger space at the center of the gears tend to minimize pulsations and give a steadier flow than the spur gear pump.
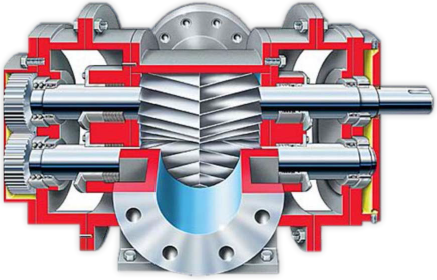
Helical Gear Pump
The helical gear pump (Figure 4-14) is another type of rotary pump. A helix is the curve produced when a straight line moves up or down the surface of a cylinder. Because of the helical gear design, the overlapping of successive discharges from spaces between the teeth produces a smooth discharge flow in the helical pump. In this type of pump, the gears can be designed with a small number of large teeth — thus allowing increased capacity without sacrificing smoothness of flow.
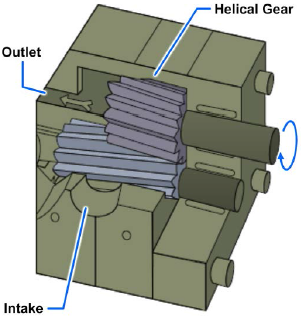
The pumping gears of this type of pump are driven by a set of timing and driving gears that help maintain the required close clearances without actual metallic contact of the pumping gears (metallic contact between the teeth of the pumping gears would provide a tighter seal against slippage; however, it would cause rapid wear of the teeth, because foreign matter in the liquid would be present on the contact surfaces).
Roller bearings at both ends of the gear shafts maintain proper alignment and minimize the friction loss in the transmission of power. Suitable packings are used to prevent leakage around the shaft.
Lobe Pump
The lobe pump uses the same principle of operation as the external gear pump described previously. The lobes are considerably larger than gear teeth, but there are only two or three lobes on each rotor. A three-lobe pump is illustrated in Figure 4-15. The two elements are rotated — one directly driven by the source of power and the other through timing gears. As the elements rotate, liquid is trapped between two lobes of each rotor and the walls of the pump chamber and carried around from the suction side to the discharge side of the pump. As liquid leaves the suction chamber, the pressure in the suction chamber is lowered and additional liquid is forced into the chamber from the reservoir.
The lobes are constructed so there is a continuous seal at the points where they meet at the center of the pump. The lobes of the pump illustrated in Figure 4-15 are fitted with small vanes at the outer edge to improve the seal of the pump. Although these vanes are mechanically held in their slots, they are, to some extent, free to move outward. Centrifugal force keeps the vanes snug against the chamber and the other rotating members.
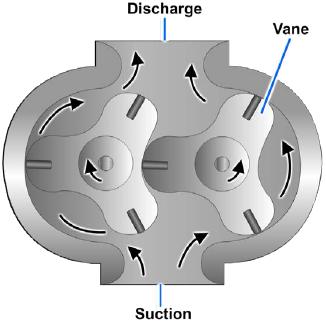
Screw Pump
Screw pumps are primarily used for pumping all viscous fluids such as JP-5 and diesel oil. Hydraulic systems on some ships use the screw pump as the pressure supply for the system. The pump may be either motor-driven or turbine-driven.
There are several types of screw pumps. The main points of difference between the various types are the number of intermeshing screws and the pitch of the screws. A positive-displacement, double-screw, low-pitch pump is illustrated in Figure 4-16. The two-screw, low-pitch screw pump has two rotors — one drive and one driven — and relies on the pumped fluid to fill the clearances between the rotor and rotors and liner. The pumped fluid seals the individual pumping chambers of the screw profiles, allowing the pump to maintain prime. One rotor has a right-handed thread, and the other rotor has a left-handed thread. One shaft is the driving shaft and drives the other shaft through a set of herringbone timing gears. Liquid is trapped at the outer end of each pair of screws. As the first space between the screw threads rotates away from the opposite screw, liquid is enclosed when the end of the screw again meshes with the opposite screw. The enclosures formed by the meshing of the rotors inside the close clearance housing contain the fluid being pumped. As the rotors turn, these enclosures move axially, providing a continuous flow. Effective performance is based on the following factors:
- The rolling action obtained with the thread design of the rotors is responsible for the very quiet pump operation. The symmetrical pressure loading around the power rotor eliminates the need for radial bearings because there are no radial loads. The cartridge-type ball bearing in the pump positions the power rotor for proper seal operation. The axial loads on the rotors created by discharge pressure are hydraulically balanced.
- The key to screw pump performance is the operation of the idler rotors in their housing bores. The idler rotors generate a hydrodynamic film to support themselves in their bores like journal bearings. Since this film is self-generated, it depends on three operating characteristics of the pump — speed, discharge pressure, and fluid viscosity. The strength of the film is increased by increasing the operating speed, by decreasing pressure, or by increasing the fluid viscosity. This is why screw pump performance capabilities are based on pump speed, discharge pressure, and fluid viscosity.
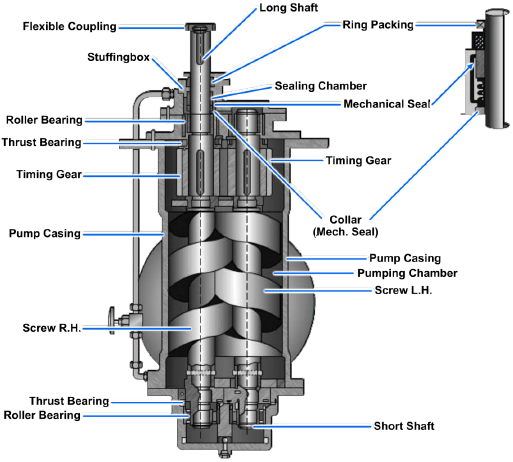
Information on the operation may be obtained from the Engineering Operating Sequencing Systems (EOSS); Naval Ships' Technical Manual (NSTM), Chapter 503; and the manufacturers' manuals. Maintenance should be performed according to Planned Maintenance System (PMS) requirements.
Vane Pump
Vane-type hydraulic pumps generally have a circular- or elliptical-shaped interior and flat end plates. Figure 4-17 illustrates a vane pump with a circular interior. A slotted rotor is fixed to a shaft that enters the housing cavity through one of the end plates. A number of small rectangular plates or vanes are set into the slots of the rotor. As the rotor turns, centrifugal force causes the outer edge of each vane to slide along the surface of the housing cavity as the vanes slide in and out of the rotor slots. The numerous cavities, formed by the vanes, end plates, housing, and rotor, enlarge and shrink as the rotor and vane assembly rotates. An inlet port is installed in the housing so fluid may flow into the cavities as they enlarge. An outlet port is provided to allow the fluid to flow out of the cavities as they become small.
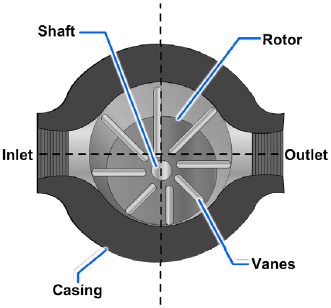
The pump shown in Figure 4-17 is referred to as an unbalanced pump because all of the pumping action takes place on one side of the rotor. This causes a side load on the rotor. Some vane pumps are constructed with an elliptical-shaped housing that forms two separate pumping areas on opposite sides of the rotor. This cancels out the side loads; such pumps are referred to as balanced vane.
Usually vane pumps are fixed-displacement and pump in only one direction. There are, however, some designs of vane pumps that provide variable flow. Vane pumps are generally restricted to service where pressure demand does not exceed 2,000 pounds per square inch (psi). Wear rates, vibration, and noise levels increase rapidly in vane pumps as pressure demands exceed 2,000 psi.
Reciprocating Pumps
The term reciprocating is defined as back-and-forth motion. In the reciprocating pump it is this back-and-forth motion of pistons inside of cylinders that provides the flow of fluid. Reciprocating pumps, like rotary pumps, operate on the positive principle — that is, each stroke delivers a definite volume of liquid to the system.
The master cylinder of the automobile brake system is an example of a simple reciprocating pump. Several types of power-operated hydraulic pumps, such as the radial piston and axial piston, are also classified as reciprocating pumps. These pumps are sometimes classified as rotary pumps, because a rotary motion is imparted to the pumps by the source of power. However, the actual pumping is performed by sets of pistons reciprocating inside sets of cylinders.
Hand Pumps
There are two types of manually operated reciprocating pumps — the single-action and the double-action. The single-action pump provides flow during every other stroke, while the double-action provides flow during each stroke. Single-action pumps are frequently used in hydraulic jacks.
A double-action hand pump is illustrated in Figure 4-18. This type of pump is used in some aircraft hydraulic systems as a source of hydraulic power for emergencies, for testing certain subsystems during preventive maintenance inspections, and for determining the causes of malfunctions in these subsystems.
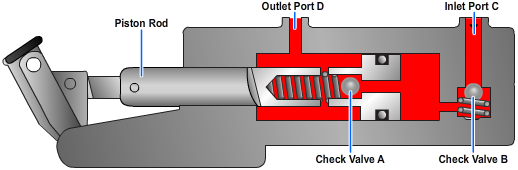
This pump (Figure 4-18) consists of a cylinder, a piston containing a built-in check valve (A), a piston rod, an operating handle, and a check valve (B) at the inlet port. When the piston is moved to the left, the force of the liquid in the outlet chamber and spring tension cause valve A to shut. This movement causes the piston to force the liquid in the outlet chamber through the outlet port and into the system. This same piston movement causes a low-pressure area in the inlet chamber. The difference in pressure between the inlet chamber and the liquid (at atmospheric pressure) in the reservoir acting on check valve B causes its spring to compress; thus, opening the check valve. This allows liquid to enter the inlet chamber.
When the piston completes this stroke to the left, the inlet chamber is full of liquid. This eliminates the pressure difference between the inlet chamber and the reservoir, thereby allowing spring tension to shut check valve B.
When the piston is moved to the right, the force of the confined liquid in the inlet chamber acts on check valve A. This action compresses the spring and opens check valve A which allows the liquid to flow from the intake chamber to the outlet chamber. Because of the area occupied by the piston rod, the outlet chamber cannot contain all the liquid discharged from the inlet chamber. Since liquids do not compress, the extra liquid is forced out of the outlet port into the system.
Piston Pumps
Piston pumps are made in a variety of types and configurations. A basic distinction is made between axial and radial pumps. The axial piston pump has the cylinders parallel to each other and the drive shaft. The radial piston design has the cylinders extending radially outward from the drive shaft like the spokes of a wheel. A further distinction is made between pumps that provide a fixed delivery and those able to vary the flow of the fluid. Variable delivery pumps can be further divided into those able to pump fluid from zero to full delivery in one direction of flow and those able to pump from zero to full delivery in either direction.
All piston pumps used in Navy shipboard systems have the cylinders bored in a cylinder block that is mounted on bearings within a housing. This cylinder block assembly rotates with the pump drive shaft.
Radial Piston Pumps
A radial pump has the pistons arranged radially in a cylinder block. The pump consists of a stationary pintle inside a circular reaction ring or rotor. As the block rotates, centrifugal force, charging pressure, or some form of mechanical action causes the pistons to follow the inner surface of the ring, which is offset from the centerline of the cylinder block. A port in the pintle permits the pistons to take in fluid as they move outward and discharge it as they move in. Pump displacement is determined by the size and number of pistons (there may be more than one bank in a single cylinder block) and the length of their stroke. A slide block is used to control the length of the piston strokes. The slide block does not revolve but houses and supports the rotor, which does revolve due to the friction set up by the sliding action between the piston heads and the reaction ring. The cylinder block is attached to the drive shaft.
Referring to Figure 4-19, view B, assume that space X in one of the cylinders of the cylinder block contains liquid and that the respective piston of this cylinder is at position 1. When the cylinder block and piston are rotated in a clockwise direction, the piston is forced into its cylinder as it approaches position 2. This action reduces the volumetric size of the cylinder and forces a quantity of liquid out of the cylinder and into the outlet port above the pintle. This pumping action is due to the rotor being off-center in relation to the center of the cylinder block.
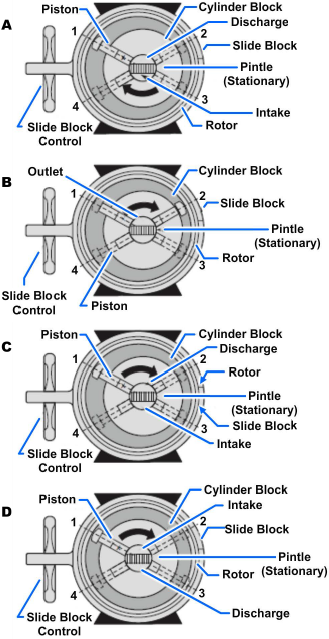
In Figure 4-19, view B, the piston has reached position 2 and has forced the liquid out of the open end of the cylinder through the outlet above the pintle and into the system. While the piston moves from position 2 to position 3, the open end of the cylinder passes over the solid part of the pintle; therefore, there is no intake or discharge of liquid during this time. As the piston and cylinder move from position 3 to position 4, centrifugal force causes the piston to move outward against the reaction ring of the rotor. During this time, the open end of the cylinder is open to the intake side of the pintle and, therefore, fills with liquid. As the piston moves from position 4 to position 1, the open end of the cylinder is against the solid side of the pintle and no intake or discharge of liquid takes place. After the piston has passed the pintle and starts toward position 2, another discharge of liquid takes place. Alternate intake and discharge continues as the rotor revolves about its axis-intake on one side of the pintle and discharge on the other, as the piston slides in and out.
Notice in Figure 4-19, view A and view B, the center point of the rotor is different from the center point of the cylinder block. The difference of these centers produces the pumping action. If the rotor is moved so that its center point is the same as that of the cylinder block, as shown in Figure 4-11, view C, there is no pumping action, since the piston does not move back and forth in the cylinder as it rotates with the cylinder block.
The flow in this pump can be reversed by moving the slide block—and therefore the rotor—to the right so the relation of the centers of the rotor and the cylinder block is reversed from the position shown in Figure 4-19, views A and B. Liquid enters the cylinder as the piston travels from position 1 to position 2 and is discharged from the cylinder as the piston travels from position 3 to 4.
In the illustrations the rotor is shown in the center, on the extreme right, or the extreme left in relation to the cylinder block. The amount of adjustment in distance between the two centers determines the length of the piston stroke, which controls the amount of liquid flow in and out of the cylinder. Thus, this adjustment determines the displacement of the pump; that is, the volume of liquid the pump delivers per revolution. This adjustment may be controlled in different ways. Manual control by a handwheel is the simplest. The pump illustrated in Figure 4-19 is controlled in this way. For automatic control of delivery to accommodate varying volume requirements during the operating cycle, a hydraulically controlled cylinder may be used to position the slide block. A gear-motor controlled by a push button or a limit switch is sometimes used for this purpose. Four pistons are shown in Figure 4-19 for the sake of simplicity.
Radial pumps are actually designed with an odd number of pistons (Figure 4-20). This is to ensure that no more than one cylinder is completely blocked by the pintle at any one time. If there were an even number of pistons spaced evenly around the cylinder block (for example, eight), there would be occasions when two of the cylinders would be blocked by the pintle, while at other times none would be blocked. This would cause three cylinders to discharge at one time and four at one time, causing pulsations in flow. With an odd number of pistons spaced evenly around the cylinder block, only one cylinder is completely blocked by the pintle at any one time. This reduces pulsations of flow.
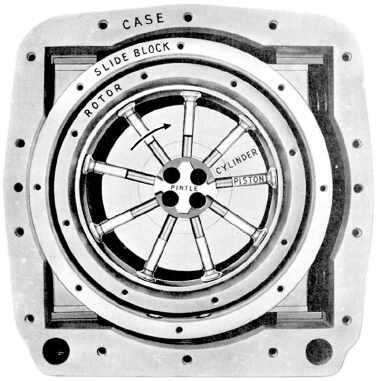
Axial Piston Pumps
The variable stroke axial-piston pump usually has either seven or nine single-acting pistons which are evenly spaced around a cylinder barrel. An uneven number of pistons are always used in order to avoid pulsations in the discharge flow. (Note that the term "cylinder barrel," as used here, actually refers to a cylinder block which holds all the cylinders.) The piston rods make a ball-and-socket connection with a socket ring. The socket ring rides on a thrust bearing carried by a casting called the tilting box or tilting block. When the tilting box is at a right angle to the shaft, and the pump is rotating, the pistons do not reciprocate; therefore, no pumping takes place. When the box is tilted away from a right angle, however, the pistons reciprocate and the liquid is pumped.
The variable stroke axial-piston pump is often used as a part of a variable speed gear such as electrohydraulic anchor windlasses, cranes, winches, and the power transmitting unit in electrohydraulic steering engines. In those cases, the tilting box is so arranged that it may be tilted in either direction. Thus it may be used to transmit power hydraulically to pistons or rams, or it may be used to drive a hydraulic motor.
In-line Axial-Piston Pump
In axial piston pumps of the in-line type where the cylinders and the drive shaft are parallel (Figure 4-21), the reciprocating motion is created by a cam plate, also known as wobble plate, tilting plate, or swash plate. This plate lies in a plane that cuts across the center line of the drive shaft and cylinder barrel and does not rotate. In a fixed-displacement pump, the cam plate will be rigidly mounted in a position so that it intersects the center line of the cylinder barrel at an angle approximately 25 degrees from perpendicular. Variable delivery axial piston pumps are designed so the angle the cam plate makes is perpendicular to the center line of the cylinder barrel and may be varied from zero to 20 or 25 degrees to one or both sides. One end of each piston rod is held in contact with the cam plate as the cylinder block and piston assembly rotates with the drive shaft. This causes the pistons to reciprocate within the cyIinders. The length of the piston stroke is proportional to the angle that the cam plate is set from perpendicular to the center line of the cylinder barrel.
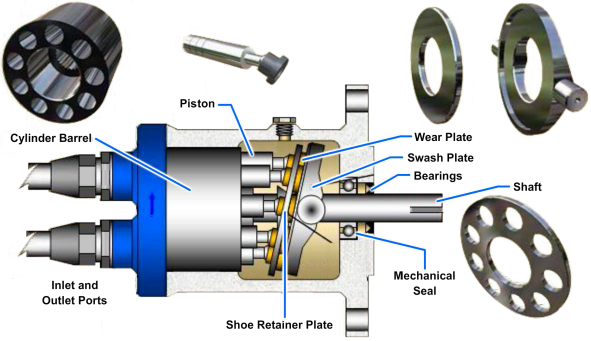
Bent Axis Piston Pump
A variation of the axial piston pump is the bent-axis type shown in Figure 4-22. This type does not have a tilting cam plate as the in-line pump. Instead, the cylinder block axis is varied from the drive shaft axis. The ends of the connecting rods are retained in sockets on a disc that turn with the drive shaft. The cylinder block is turned with the drive shaft by a universal joint assembly at the intersection of the drive shaft and the cylinder block shaft. In order to vary the pump displacement, the cylinder block and valve plate are mounted in a yoke and the entire assembly is swung in an area around a pair of mounting pintles attached to the pump housing.
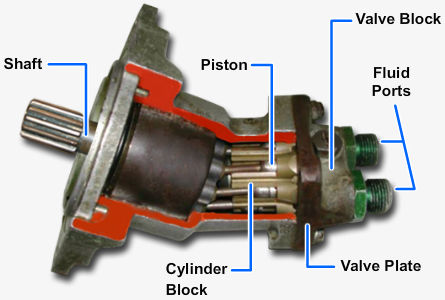
The bent axis piston pump is capable of operating at variable conditions of flow, pressure, speed, and torque. The major elements of bent axis piston pump are pistons, connecting rods, universal joint, flanges, input shaft, output shaft, bearings, and motor.
Bent axis piston pumps tend to be slightly more volumetrically efficient. One end of each piston is held in contact with the cam plate as the cylinder block and piston assembly rotates with the drive shaft. This causes the pistons to reciprocate within the cylinders. The length of the piston stroke is proportional to the angle that the cam plate makes with the pump center line. Another characteristic of a piston-type pump is that the displacement can be changed simply by changing the angle of the swash plate. Any displacement between zero and maximum is achieved with simple actuators to change the swash plate angle. The displacement-varying mechanism and power-to-weight ratio of the variable displacement piston pump makes them most suitable for control of high power levels.
First, a rocker arm is installed on a horizontal shaft (Figure 4-23, view A). The arm is joined to the shaft by a pin so that it can be swung back and forth, as indicated in Figure 4-23, view B. Next, a ring is placed around the shaft and secured to the rocker arm so the ring can turn from left to right as shown in Figure 4-23, view C. This provides two rotary motions in different planes at the same time and in varying proportions as may be desired. The rocker arm can swing back and forth in one arc, and the ring can simultaneously move from left to right in another arc, in a plane at right angles to the plane in which the rocker arm turns.
Next, a tilting plate is added to the assembly. The tilting plate is placed at a slant to the axis of the shaft, as depicted in Figure 4-23, view D. The rocker arm is then slanted at the same angle as the tilting plate, so that it lies parallel to the tilting plate. The ring is also parallel to, and in contact with, the tilting plate. The position of the ring in relation to the rocker arm is unchanged from that shown in Figure 4-23, view C.
Figure 4-23, view E, shows the assembly after the shaft — still in a horizontal position — has been rotated a quarter turn. The rocker arm is still in the same position as the tilting plate and is now perpendicular to the axis of the shaft. The ring has turned on the rocker pins, so that it has changed its position in relation to the rocker arm, but it remains parallel to — and in contact with — the tilting plate.
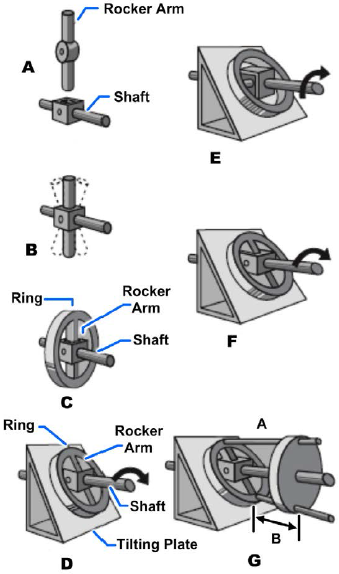
Figure 4-23, view F, shows the assembly after the shaft has been rotated another quarter turn. The parts are now in the same position as shown in Figure 4-23, view D, but with the ends of the rocker arm reversed. The ring still bears against the tilting plate.
As the shaft continues to rotate, the rocker arm and the ring turn about their pivots, with each changing its relation to the other and with the ring always bearing on the plate.
Figure 4-23, view G, shows a wheel added to the assembly. The wheel is placed upright and fixed to the shaft, so that it rotates with the shaft. In addition, two rods (A and B) are loosely connected to the tilting ring and extend through two holes standing opposite each other in the fixed wheel. As the shaft is rotated, the fixed wheel turns perpendicular to the shaft at all times. The tilting ring rotates with the shaft and always remains tilted, since it remains in contact with the tilting plate. Referring to Figure 4-23, view G, the distance along rod A from the tilting ring to the fixed wheel, is greater than the distance along rod B. As the assembly is rotated, however, the distance along rod A decreases as its point of attachment to the tilting ring moves closer to the fixed wheel, while the distance along rod B increases. These changes continue until after a half revolution, at which time the initial positions of the rods have been reversed. After another half revolution, the two rods will again be in their original positions.
As the assembly rotates, the rods move in and out through the holes in the fixed wheel. This is the way the axial piston pump works. To get a pumping action, pistons are placed at the ends of the rods beyond the fixed wheel, and inserted into cylinders. The rods must be connected to the pistons and to the wheel by ball and socket joints. As the assembly rotates, each piston moves back and forth in its cylinder. Suction and discharge lines can be arranged so that liquid enters the cylinders while the spaces between the piston heads and the bases of the cylinders are increasing, and leaves the cylinders during the other half of each revolution when the pistons are moving in the opposite direction.
The main parts of the pump are the drive shaft, pistons, cylinder block, and valve and swash plates. There are two ports in the valve plate. These ports connect directly to openings in the face of the cylinder block. Fluid is drawn into one port and forced out the other port by the reciprocating action of the pistons.
Stratopower Pump
Another type of axial piston pump, sometimes referred to as an in-line pump, is commonly referred to as a Stratopower pump. This pump is available in either the fixed-displacement type or the variable-displacement type.
Two major functions are performed by the internal parts of the fixed-displacement Stratopower pump. These functions are mechanical drive and fluid displacement.
The mechanical drive mechanism is shown in Figure 4-24. In this type of pump, the pistons and block do not rotate. Piston motion is caused by rotating the drive cam, displacing each piston the full height of the drive cam during each revolution of the shaft. The ends of the pistons are attached to a wobble plate supported by a freed center pivot and are held in constant contact with the cam face. As the high side of the rotating drive cam depresses one side of the wobble plate, the other side of the wobble plate is withdrawn an equal amount, moving the pistons with it. The two creep plates are provided to decrease wear on the revolving cam.
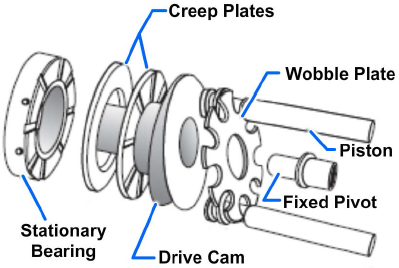
A schematic diagram of the displacement of fluid is shown in Figure 4-25. Fluid is displaced by axial motion of the pistons. As each piston advances in its respective cylinder block bore, pressure opens the check valve and a quantity of fluid is forced past it. Combined back pressure and check valve spring tension shut the check valve when the piston advances to its foremost position. The low-pressure area occurring in the cylinder during the piston return causes fluid to flow from the reservoir into the cylinder.
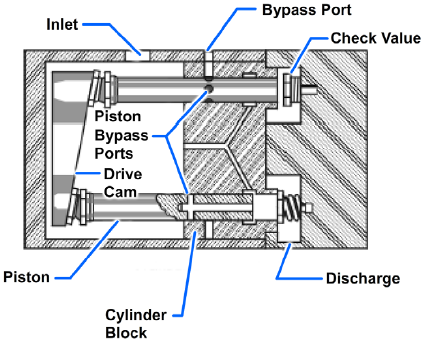
The internal features of the variable-displacement Stratopower pump are illustrated in Figure 4-26. This pump operates similarly to the fixed-displacement Stratopower pump; however, this pump provides the additional function of automatically varying the volume output.
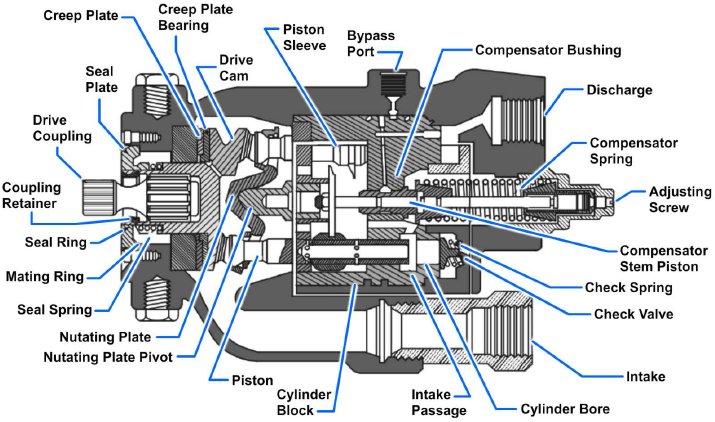
This function is controlled by the pressure in the hydraulic system. For example, a pump rated at 3,000 psi provides flow to a 3,000 psi system. As system pressure approaches 2,850 psi, the pump begins to unload (delivering less flow to the system) and is fully unloaded (zero flow) at 3,000 psi.
The pressure regulation and flow are controlled by internal bypasses that automatically adjust fluid delivery to system demands.
The bypass system is provided to supply self-lubrication, particularly when the pump is in nonflow operation. The ring of bypass holes in the pistons are aligned with the bypass passage each time a piston reaches the very end of its forward travel. This pumps a small quantity of fluid out of the bypass passage back to the supply reservoir and provides a constant change of fluid in the pump. The bypass is designed to pump against a considerable back pressure for use with pressurized reservoirs.
Eductors
Eductors (Figure 4-27) are designed to pump large volumes of water. In modern ships, eductors have replaced fire and bilge pumps as a primary means for pumping bilges, deballasting, and dewatering compartments. Eductors allow centrifugal fire pumps to serve indirectly as drainage pumps without the risk of becoming fouled with debris from the bilges. The centrifugal pumps pressurize the fire main, and water from the fire main is used to actuate the eductors. The eductors in modern combat ships have a much larger pumping capacity than fire and bilge pumps. They are installed as part of the piping in the drainage system and are flanged to permit easy removal and disassembly when repairs are necessary.
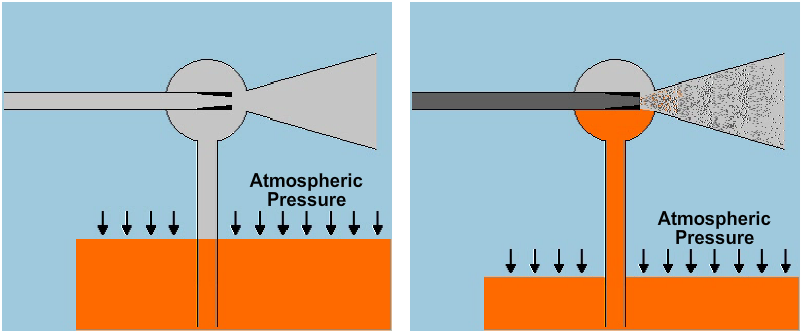
Improper lighting off and securing of an eductor can cause rapid flooding of the space being pumped. Always follow the proper procedure!
PDH Classroom offers a continuing education course based on this hydraulic pumps reference page. This course can be used to fulfill PDH credit requirements for maintaining your PE license.
Now that you've read this reference page, earn credit for it!