Anisotropic Pressure Vessels
This page provides the section on anisotropic pressure vessels from the "Stress Analysis Manual," Air Force Flight Dynamics Laboratory, October 1986.
Other related chapters from the Air Force "Stress Analysis Manual" can be seen to the right.
- Simple Thin Pressure Vessels
- Stiffened Thin Pressure Vessels
- Thick Pressure Vessels
- Anisotropic Pressure Vessels
8.5 Anisotropic Pressure Vessels
The use of glass filaments in the construction of pressure vessels offers several advantages. Glass has an ultimate strength of approximately 300,000 lb/in2 in the direction of the fiber when it is drawn into fine filaments. In order to fully utilize this high unidirectional strength, however, it is necessary to run the fiber in the direction of the maximum principal stress. This is done by winding the fibers on a mandrel. During the winding process, the filaments are impregnated with resin which, after curing, will develop sufficient shear strength to realize the high tensile strength of the fibers. In analyzing these structures, it is assumed that the fibers sustain the primary loads with only the secondary loads being resisted by the resin binder.
Since the principal stresses will vary in an actual vessel, the fibers may actually be wrapped at more than a single wrap angle as may be seen in Figure 8-52.
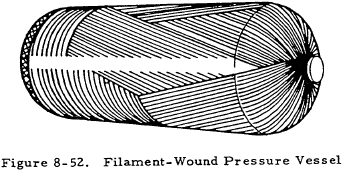
For a thin cylindrical pressure vessel, all stresses other than membrane stresses are negligible. The optimum wrap angle is 55 degrees as shown in Figure 8-53.
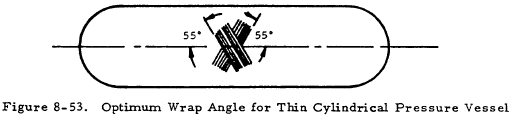
In addition to providing a structure of high strength-to-weight ratio, the glass pressure vessels offer other advantages. Connections can be eliminated and end closures, skirts, etc., fabricated as a single unit. In addition, pressure vessels may be made in any proportions and sizes over wide ranges.