Rivets and Lockbolts
This page provides the sections on rivets and lockbolts from Barrett, "Fastener Design Manual," NASA Reference Publication 1228, 1990.
Other related chapters from the NASA "Fastener Design Manual" can be seen to the right.
- Fastener Design Criteria
- Fastener Torque
- Loads on Fastener Groups
- Fatigue Resistant Bolts
- Rivets and Lockbolts
Rivets and Lockbolts
Rivets
Rivets are relatively low-cost, permanently installed fasteners that are lighter weight than bolts. As a result, they are the most widely used fasteners in the aircraft manufacturing industry. They are faster to install than bolts and nuts, since they adapt well to automatic, high-speed installation tools. However, rivets should not be used in thick materials or in tensile applications, as their tensile strengths are quite low relative to their shear strengths. The longer the total grip length (the total thickness of sheets being joined), the more difficult it becomes to lock the rivet.
Riveted joints are neither airtight nor watertight unless special seals or coatings are used. Since rivets are permanently installed, they have to be removed by drilling them out, a laborious task.
General Rivet Types
The general types of rivets are solid, blind, tubular, and metal piercing (including split rivets). From a structural design aspect the most important rivets are the solid and blind rivets.
Solid rivets.-- Most solid rivets are made of aluminum so that the shop head can be cold formed by bucking it with a pneumatic hammer. Thus, solid rivets must have cold-forming capability without cracking. A representative listing of solid rivets is given in table IX (ref. 2). Some other solid rivet materials are brass, SAE 1006 to SAE 1035, 1108 and 1109 steels, A286 stainless steel, and titanium.
Material | Rivet designation |
Rivet heads available |
Applications |
---|---|---|---|
2117-T4 | AD | Universal (MS20470) 100° Flush (MS20426) |
General use for most applications |
2024-T4 | DD | Universal (MS20470) 100° Flush (MS20426) |
Use only as an alternative to 7050-T73 where higher strength is required |
1100 | A | Universal (MS20470) 100° Flush (MS20426) |
Nonstructural |
5056-H32 | B | Universal (MS20470) 100° Flush (MS20426) |
Joints containing magnesium |
Monel (annealed) |
M | Universal (MS20615) 100° Flush (MS20427) |
Joining stainless steels, titanium, and Inconel |
Copper (annealed) |
--- | 100° Flush (MS20427) | Nonstructural |
7050-T73 | E | Universal (MS20470) 100° Flush (MS20426) |
Use only where higher strength is required |
Note that the rivets in table IX are covered by military standard specifications, which are readily available. Although most of the solid rivets listed in table IX have universal heads, there are other common head types, as shown in figure 34. However, because the "experts" do not necessarily agree on the names, other names have been added to the figure. Note also that the countersunk head angle can vary from 60° to 120° although 82° and 100° are the common angles.

The sharp edge of the countersunk head is also removed in some cases, as in the Briles BRFZ "fast" rivet (fig. 35), to increase the shear and fatigue strength while still maintaining a flush fit.
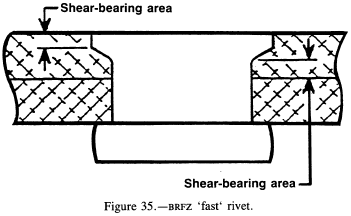
Blind rivets.-- Blind rivets get their name from the fact that they can be completely installed from one side. They have the following significant advantages over solid rivets:
- Only one operator is required for installation.
- The installation tool is portable (comparable to an electric drill in size).
- They can be used where only one side of the workpiece is accessible.
- A given-length rivet can be used for a range of material thicknesses.
- Installation time is faster than with solid rivets.
- Clamping force is more uniform than with solid rivets.
- Less training is required for the operator.
Blind rivets are classified according to the methods used to install them:
- Pull mandrel
- Threaded stem
- Drive pin
Specific types (brands) of blind rivets are covered in subsequent sections of this manual.
Pull-mandrel rivets: This rivet is installed with a tool that applies force to the rivet head while pulling a prenotched serrated mandrel through to expand the far side of the tubular rivet. When the proper load is reached, the mandrel breaks at the notch. A generic pull-mandrel rivet is shown in figure 36.

Threaded-stem rivets: The threaded-stem rivet (fig. 37(a)) has a threaded internal mandrel (stem) with the external portion machined flat on two sides for the tool to grip and rotate. The head is normally hexagonal to prevent rotation of the tubular body while the mandrel is being torqued and broken off.
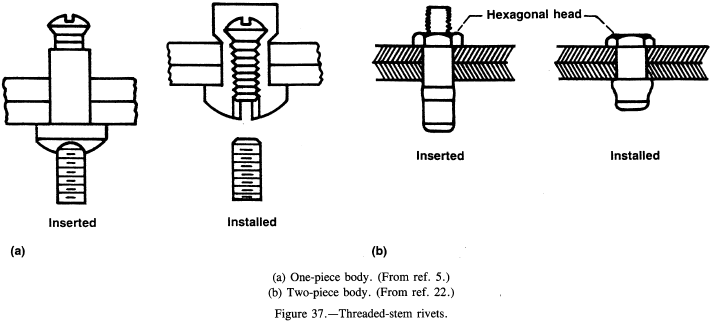
Drive-pin rivets: This rivet has a drive pin that spreads the far side of the rivet to form a head, as shown in figure 38. Although drive-pin rivets can be installed quickly, they are usually not used in aerospace applications. They are used primarily for commercial sheet metal applications.

Tubular rivets.-- Tubular rivets are partially hollow and come in a variety of configurations. The generic form has a manufactured head on one side and a hollow end that sticks through the pieces being joined. The hollow end is cold formed to a field head.
Since extensive cold forming is required on these rivets, they must be extremely ductile and are consequently made of lowstrength materials. They are normally used for commercial applications rather than in the aerospace industry.
Some specific types of tubular rivets are
- Compression
- Semitubular
- Full tubular
Compression tubular rivets: A compression tubular rivet (fig. 39) consists of two parts that have an interference fit when driven together. These rivets are used commercially in soft materials and where a good appearance is required on both sides of the part.
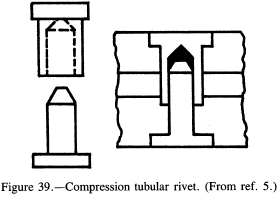
Semitubular rivets: The semitubular rivet (fig. 40) has a hole in the field end (hole depth to 1.12 of shank diameter) such that the rivet approaches a solid rivet when the field head is formed.

Full tubular rivets: The full tubular rivet (fig. 41) has a deeper hole than the semitubular rivet. It is a weaker rivet than the semitubular rivet, but it can pierce softer materials such as plastic or fabric.

Metal-piercing rivets.-- Metal piercing rivets (fig. 42) are similar to semitubular rivets, except that they have greater column strength. Part of the sandwich material is not drilled, and the rivet pierces all the way or most of the way through while mushrooming out to a locked position.

Split rivets.-- Split (bifurcated) rivets (fig. 43) are the standard "home repair" rivets. They have sawed or split bodies with sharp ends to make their own holes through leather, fiber, plastic, or soft metals. They are not used in critical applications.

Need a Bolted Joint Calculator?
Try this bolted joint calculator.
- stress analysis of a bolted joint
- accounts for preload, applied axial load, and applied shear load
Specific Rivet Types
AD & DD solid rivets.-- The most common solid rivets are the AD and DD aluminum rivets, as listed in table IX. These are the preferred rivets for joining aluminums and combinations of aluminum and steel. The "icebox" (DD) rivets can be used in higher-strength applications, but they must be kept around 0 °F until they are installed. The 7050-T73 aluminum rivets are an alternative to "icebox" rivets.
Since solid rivets are expanded to an interference fit, they should not be used in composites or fiber materials. They can cause delamination of the hole surfaces, leading to material failure.
Cherry Buck rivets.-- The Cherry Buck rivet is a hybrid consisting of a factory head and shank of 95-ksi-shear-strength titanium, with a shop end shank of ductile titanium/niobium joined together by inertia welding (fig. 44). This combination allows a shop head to be formed by bucking, but the overall shear strength of the rivet approaches 95 ksi. The Cherry Buck rivet can be used to 600 °F.

Monel rivets.-- Monel (67 percent nickel and 30 percent copper) rivets are used for joining stainless steels, titanium, and Inconel. Monel is ductile enough to form a head without cracking but has higher strength (Fsu = 49 ksi) and temperature capabilities than aluminum.
Titanium/niobium rivets.-- These titanium alloy rivets (per MIL-R-5674 and AMS4982) have a shear strength of 50 ksi but are still formable at room temperature. They generally do not need a coating for corrosion protection. The Cherry E-Z Buck is a titanium/niobium rivet.
Cherry rivets.-- The generic Cherry rivet is a blind structural rivet with a locking collar for the stem installed as shown in figure 45. (Different head types are available.) Cherry rivets are available in both nominal and oversize diameters in the common (1/8 through 1/4 in.) sizes. The oversize rivets are used for repairs where a nominal-size rivet (solid or blind) has been drilled out or where the initial drilled hole is oversize. These rivets have shear strengths comparable to AD solid aluminum rivets. However, their usage is restricted in aircraft manufacturing by the guidelines of MS33522, which is included as appendix C. A typical list of available Cherry rivet materials is shown in table X.
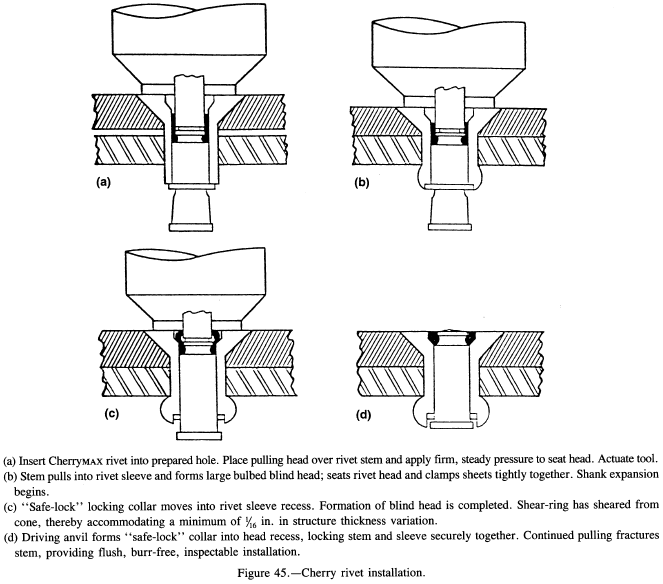
Materials | Ultimate shear strength, psi |
Maximum temperature, °F |
|
---|---|---|---|
Sleeve | Stem | ||
5055 Aluminum | Alloy steel | 50,000 | 250 |
5056 Aluminum | CRES | 50,000 | 250 |
Monel | CRES | 55,000 | 900 |
Inco 600 | Inco X750 | 75,000 | 1400 |
Huck blind rivets.-- Huck blind rivets are similar to Cherry rivets, except that they are available in higher strength material. These rivets are made with and without locking collars and with countersunk or protruding heads. Note also (in fig. 46) that the sleeve on the blind side is deformed differently on the Huck rivet than on the Cherry rivet.

Pop rivets.-- Pop rivets are familiar to most of the public for home repairs. However, they are not recommended for critical structural applications. The stem sometimes falls out of the sleeve after the rivet is installed, and the symmetry of the blind (formed) head leaves much to be desired. Although the pop rivet shown in figure 47 is the most common type, USM makes a closed-end rivet and three different head styles.

Need a Bolted Joint Calculator?
Try this bolted joint calculator.
- stress analysis of a bolted joint
- accounts for preload, applied axial load, and applied shear load
Lockbolts
In general, a lockbolt is a nonexpanding, high-strength fastener that has either a swaged collar or a type of threaded collar to lock it in place. It is installed in a standard drilled hole with a snug fit but normally not an interference fit. A lockbolt is similar to an ordinary rivet in that the locking collar or nut is weak in tension loading and is difficult to remove once installed.
Some of the lockbolts are similar to blind rivets and can be completely installed from one side. Others are fed into the workpiece with the manufactured head on the far side. The installation is then completed from the near side with a gun similar to blind rivet guns. Lockbolts are available with either countersunk or protruding heads.
Since it is difficult to determine whether a lockbolt is installed properly, they should be used only where it is not possible to install a bolt and nut of comparable strength. However, they are much faster to install than standard bolts and nuts.
Jo-Bolts
Jo-bolts are similar to blind rivets in appearance and installation. The locking collar (sleeve) is expanded to form a shop head by rotating the threaded stem with a gun. The threaded stem is notched and breaks off when the proper torque is reached. A typical Jo-bolt installation is shown in figure 48.
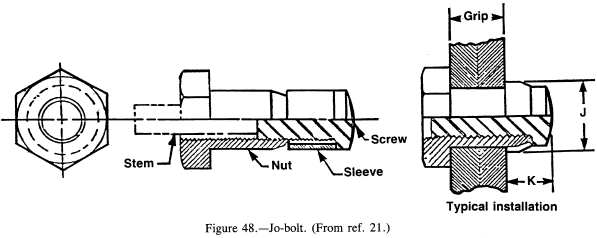
Hi-Lok
The Hi-Lok lockbolt has a countersunk or protruding manufactured head and threads like a bolt. It is fed through the hole from the far side. The installation gun prevents shank rotation with a hexagonal key while the nut is installed (as shown in fig. 49). The nut (collar) hexagonal end is notched to break off at the desired torque. Hi-Lok lockbolts are available in high-strength carbon steel (to 156-ksi shear), stainless steel (to 132-ksi shear), and titanium (to 95-ksi shear).
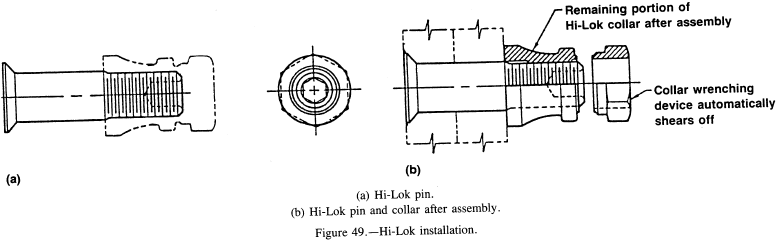
Huckbolts
Huckbolts are similar to Hi-Loks except that the stem is usually serrated rather than threaded. The collar is swaged on the stem. Then the stem is broken at the notch as shown in figure 50. Huckbolts and their collars are available in carbon steel, aluminum, and stainless steel with various strengths, as listed in the Huck catalog.

Taper-Lok
Taper-Lok is a high-strength threaded fastener that is installed with an interference fit. Most of the shank is tapered on a 1.19° angle. The lubricated lockbolt is driven into a drilled and reamed hole. The interference fit allows the nut (tension or shear nut) to be installed and torqued to the required value without holding the lockbolt to prevent rotauon (see fig. 51). The nuts are locknuts with captive washers. When a tension nut is installed, this fastener can take as much tension load as a bolt of the same size and material. Consequently, Taper-Loks are used in critical applications where cyclic loading is a problem. Taper-Lok lockbolts are available in high-strength alloy steel, H-11 tool steel, and several stainless steels, as well as titanium.

Rivnuts
A Rivnut is a tubular rivet with internal threads that is deformed in place to become a blind nutplate (fig. 52). Rivnuts are available with protruding, countersunk, and fillister heads. They are also available with closed ends, sealed heads, ribbed shanks, hexagonal shanks, and ribbed heads. Since the unthreaded tubular portion of the rivet must deform, the material must be ductile. Consequently, the Rivnut materials are fairly low strength, as shown in table XI.

Material | Type | Standard finish | Minimum ultimate tensile strength, psi |
---|---|---|---|
Aluminum | 6053-T4 | Anodize -- Alumilite 205 will meet specifications: MIL-A-8625 (ASG) | 28,000 |
Steel | C-1108 (Note 1) C-1110 (Note 1) |
Cadmium plate -- 0.0002 in. minimum thickness per QQ-P-416b, class 3, type I | 45,000 |
4037 | Cadmium plate -- 0.0002 in. minimum thickness per QQ-P-416b, class 2, type II | 55,000 (Note 2) 85,000 (Note 3) |
|
Stainless steel | 430 | Pickled and passivated per QQ-P-35, type II | 67,000 |
305 (Note 4) Carpenter 10 (Note 4) |
None -- bright as machined | 80,000 | |
Brass | Alloy 260 | None -- bright as machined | 50,000 |
Note 1: C-1108 and C-1110 steel may be used interchangeably. | |||
Note 2: No. 4 and No. 6 thread sizes. | |||
Note 3: No. 8 - 1/2-in. thread size. | |||
Note 4: 305 and Carpenter No. 10 stainless steel may be used interchangeably. |
Hi-Shear Rivet
Hi-Shear rivets consist of a high-strength carbon steel, stainless steel, aluminum, or titanium rivet (pin) with a necked-down shop head, as shown in figure 53. The collar (2024 aluminum or Monel) is swaged on to give a finished head that can be visually inspected for proper form. This rivet should be used for shear applications only, as the collar has negligible tensile strength.
Although this rivet has been partially superseded by various lockbolts, it is still being used in aircraft and aerospace applications.

Lightweight Grooved Proportioned Lockbolt
The lightweight grooved proportioned lockbolt (LGPL) is made especially for composite materials. It has both an oversize head and an oversize collar to lessen contact stresses on the composite material during both installation and service life. The shank is high-strength (95-ksi shear) titanium and the collar is 2024 aluminum. It is installed with a lockbolt tool as shown in figure 54.

Need a Bolted Joint Calculator?
Try this bolted joint calculator.
- stress analysis of a bolted joint
- accounts for preload, applied axial load, and applied shear load
General Guidelines for Selecting Rivets and Lockbolts
A number of standard documents are available for the selection, installation, and drawing callout of rivets and lockbolts as follows:
- Rivet installations are covered by MIL-STD-403. This specification covers pilot holes, deburring, countersinking, dimpling, and the application of zinc chromate paint between dissimilar materials. Other specifications for corrosion prevention of drilled or countersunk surfaces are covered in MIL-P-116 and MIL-STD-171.
- Design and selection requirements for blind structural rivets are given in MS33522 (appendix C).
- Design and selection requirements for blind nonstructural rivets are given in MS33557.
- A wealth of information on allowable rivet strengths in various materials and thicknesses is given in chapter 8 of MIL-HDBK-5 (ref. 1).
- Testing of fasteners is covered by MIL-STD-1312.
- Lockwiring is done per MS33540.
Note that the nominal rivet spacing for a rivet pattern is an edge distance of 2D and a linear spacing of 4D, where D is the rivet diameter. However, the 4D spacing can be increased if sealing between rivets or interrivet buckling is not a problem.
Solid rivets (expanded during installation) should not be used in composite materials, as they can overstress the hole and cause delamination of the material.
References
- Metallic Materials and Elements for Aerospace Vehicle Structures. MIL-HDBK-5E, Department of Defense, June 1987.
- Design Handbook, Section 16. McDonnell Douglas Astronautics Co., Huntington Beach, CA.